株式会社TASKO 成田敬様よりお話を伺いました。株式会社TASKOは舞台制作・機械製作・デザイン・マネジメントを専門とするアートカンパニーです。DMM.make 3Dプリントサービスで造形サイズと個数の課題を解決した事例をご紹介いたします。
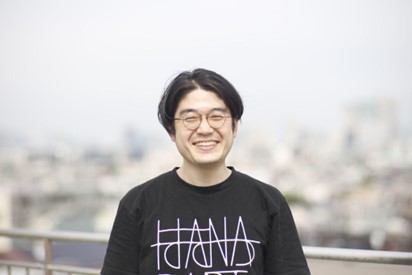
【成田敬様 プロフィール】
株式会社TASKO設計製作部 演出企画・設計担当。2019年入社。
各種ディスプレイや展示会の動いたり光ったりする演出装置を企画、設計をしています。
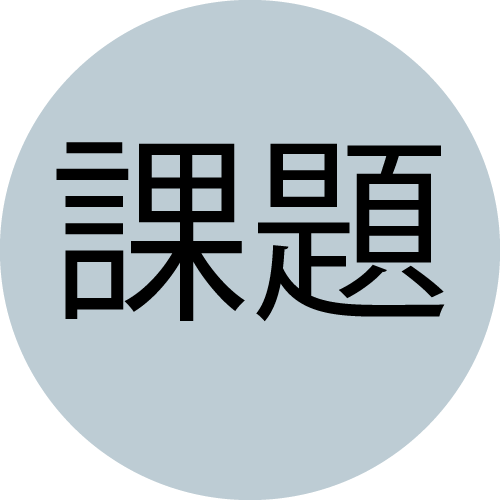
サイズが160mmくらいのローラーが全部で100台くらい必要だった。自社所有の3Dプリンターでの作成は納期的とサイズ的に厳しかった。
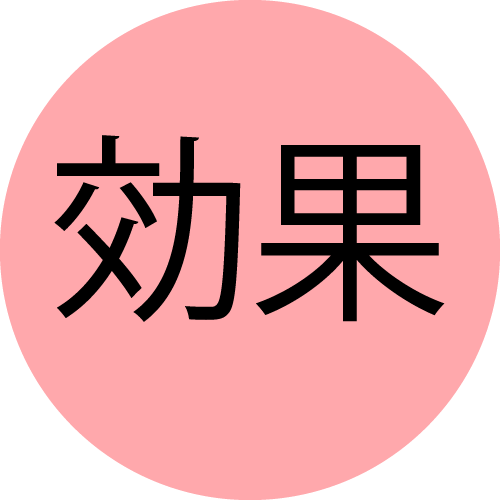
複雑な造形ができる、コスト削減、納期短縮
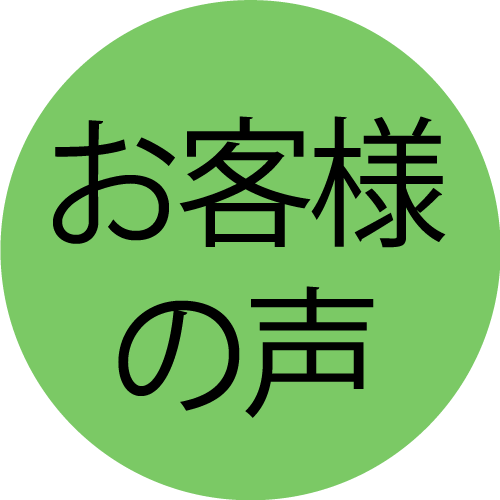
掘削だと形状的にかなり複雑で、パーツを分割すると接合などの手間もあって、100個も作るとなると人件費の問題もあります。
接合部分が外れてしまうリスクもあったので、諸々を考慮して3Dプリンターで出力するのが一番良いだろうという判断でしたね。
会社概要について
本日はよろしくお願いいたします。
さっそく、御社の事業内容を簡単にご紹介いただけますでしょうか。
弊社は株式会社TASKOという会社で、6つの部署に分かれて事業を行っています。
プロデュース事業部、制作事業部、美術部、舞台制作事業部、設計制作事業部、デザイン&ウェブ事業部とありまして、自分がいるのは設計制作事業部です。
設計制作事業部では、基本的には電飾や機械の制作開発を行っていて、舞台やアーティストとのコラボレーションで美術制作を行うこともあります。
かなり手広く事業を行われているのですね。
そうですね。
オリジナルで制作・開発した機械の販売やレンタルを行う一方で、ディレクション業務や企画立案といったプランニングも行っています。
業種としてはかなり幅が広くて、センサーを取り付けてそれと連動させたり、時には舞台や撮影美術のチームとコラボしたりもしますね。
いろいろな方法で動かしたり光らせたりといった演出を行っていくのが主な業務です。
ありがとうございます。
オリジナルの機械の制作と販売というお話がありました。具体的にどのようなものになるでしょうか。
設計制作事業部として代表的なものはHigatrecという筋トレマシンですかね。
比嘉一雄さんというパーソナルトレーナーの方が提唱する筋力トレーニング方法を、再現したものになります。
筋力トレーニングマシンというと、ウェイトを付けたり外したりするものですか?
一般的にはそういうイメージですよね。
普通のウェイトトレーニングのように毎回同じ負荷がかかるのではなく、上げるときや下げるとき、筋力の疲労状況、その時々で重さを柔軟に変えられることが理想的。
そういったトレーニング理論があって、それに対応している筋力トレーニングマシンを作ろうという話から始まりました。
これは、モーターで制御する機構を取り入れた筋トレマシンで、モーターの負荷でトレーニングの重量設定ができます。
最初に自分の筋肉量を計測して、1回目と2回目の差を記録することで、その結果に基づいて常に筋力量の負荷を変え続けるというものです。
こういった製品の技術的なディレクションや開発のお手伝いをする事業部ですね。
非常にユニークな見た目で、光の演出もかっこいいですね。
演出もこだわっています。
最近はこのマシンが使えるパーソナルジムの内装も担当しています。
取り組まれていることが非常に幅広いですが、それぞれの技術を持った人が御社に集まっているようなイメージでしょうか。
割とそうですね。幅広いスキルを持った人が集まっていると思います。
横のつながりも多くて、弊社だと映像制作は他の会社に発注して、そこと協業する形で取り組むことも多いです。
3Dプリンターを利用するシチュエーション
DMMでご利用いただいたように、3Dプリンターを業務で利用されるシーンは多いのでしょうか。
弊社でも3Dプリンターを持っていて、自分たちで設計して作ることも多いですね。
自分たちで作れる範囲であれば、毎日動かしているような状況です。
3Dプリンターをお持ちなのですね。
どのような機種を何台くらい導入されているのでしょうか。
UPさんの少し小さめのモデルで、150×150mmくらいの造形ができるものが3台あります。
あと、Zortraxさんの200×200mmくらいの機種を1台持っています。
なるほど。
社員の方が毎日オフィスに出社して、ものを生産しているイメージでしょうか。
武蔵小山に本社があって、それとは別に溝の口にファクトリーがあります。
最近では社内でリモートワークも進んでいますね。
プランニングや設計だけの場合はリモートで、ということが多いです。
オフィスが2箇所にあるんですね。
そうですね。
ファクトリーのほうが大きいフロアで、基本的にそちらでモノづくりをしています。
一見すると様々な部品や材料で溢れかえっている会社です(笑)
3Dプリンターの活用は、会社が始まった頃から取り組まれていたのでしょうか。
自分が入社したのは会社が設立してから5〜6年くらい経ってからですが、恐らくかなり早い段階で3Dプリンターを導入していたと思います。
CADを使った3Dデータの制作は、それ専門の人がいる感じでしょうか。
設計する人それぞれが自分で作っていますね。
みなさんが3Dモデルを作れるスキルを持っているのですね。
制作物の計画を練る際、3Dプリンター以外の金型や切削などの方法も検討されることはございますか?
検討しますね。
制作物の計画ができた時、それを作るための効率の良い方法を社内で話し合っています。
どういった作品だと3Dプリンターが採用されやすいでしょうか。
そうですね……。基本的には有機的な形状のものを作るときに3Dプリンターが選ばれやすいですかね。
プロジェクトにもよりますが、切削は時間もコストもかかってしまいますし……。
あと、既製品を接合するような形だと、強度的に弱くなってしまう問題も出てくるので、サイズが大きいものも一体で作れる3Dプリンターが選ばれやすいですね。
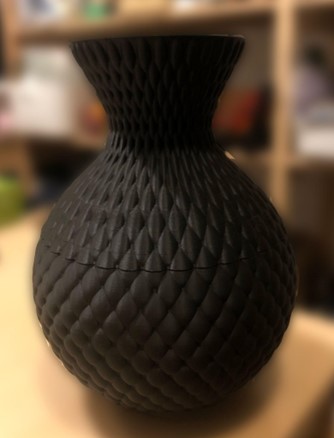
※今回紹介の案件には関係ありません
3Dプリントの外注サービスを利用するケース
社内の3Dプリンターは、主に試作用として使われるのでしょうか。
もしくは、本番用のものとして使われることもございますか?
基本的には試作が多いですが、案件によっては本番で使うこともあります。
精密性を求めない場合や安全性がそこまで必要ないもの、展示期間が短い場合は社内で作ったものを納めています。
精密性が関わってくる場合は外注するケースも多いです。
精密性が問われるというのは、どういうシチュエーションでしょうか。
たとえば、何かを固定するためのパーツを作るような場合ですね。
固定している部分の寸法が違って、外れて落ちてしまうと大問題になります。
そういう場合は3Dプリンターにしないという選択肢もありますが、案件によりけりといったところです。
そういうシチュエーションのときに、我々のような外注業者をご利用されるということですね。
そうですね。あと、外注する際の主な理由としてはサイズもありますね。
弊社の3Dプリンターだと大きくても200×200mmくらいまでしか出せないので…。
(200×200×200mmのプリンターは最近導入されました)
2つに分割して出力して後からくっつける方法だと、手間もかかるし精度も落ちてしまうので、サイズが大きいものを量産するときに外注するという印象です。
サイズが大きいもので量産が必要な場合もあるのでしょうか?
ありますね。
たとえば、以前とある案件で、実際の紙がパラパラ動く装置に映像を投影する装置を制作しました。
円柱型のロール部分にモーターを取り付けて、時刻表みたいに紙がどんどんめくれる機構になっています。
そこに3Dプリンターで作ったプロダクトを利用したのですが、サイズが160mmくらいのローラーが全部で100台くらい必要でした。
(当時はW150×D150×H120mmが社内にあるプリンターでの最大サイズでした)
弊社のプリンターではサイズも大きく、納期も間に合わず、どうしても発注したかったということがあります。
なるほど。
3Dプリンター以外の方法を検討するケースもあるとのことでしたが、ローラー部分は3Dプリンターで作ると最初から決まっていたのでしょうか。
このときは一枚一枚の紙に一本ずつ芯材が入っていて、それを小さな穴がたくさん空いたローラーに取り付ける形でした。
掘削だと形状的にかなり複雑で、パーツを分割すると接合の手間もあって、100個も作るとなると人件費の問題もありました。
接合部分が作動中に外れてしまうリスクもあったので、諸々を考慮して3Dプリンターで出力するのが一番良いだろうという判断でした。
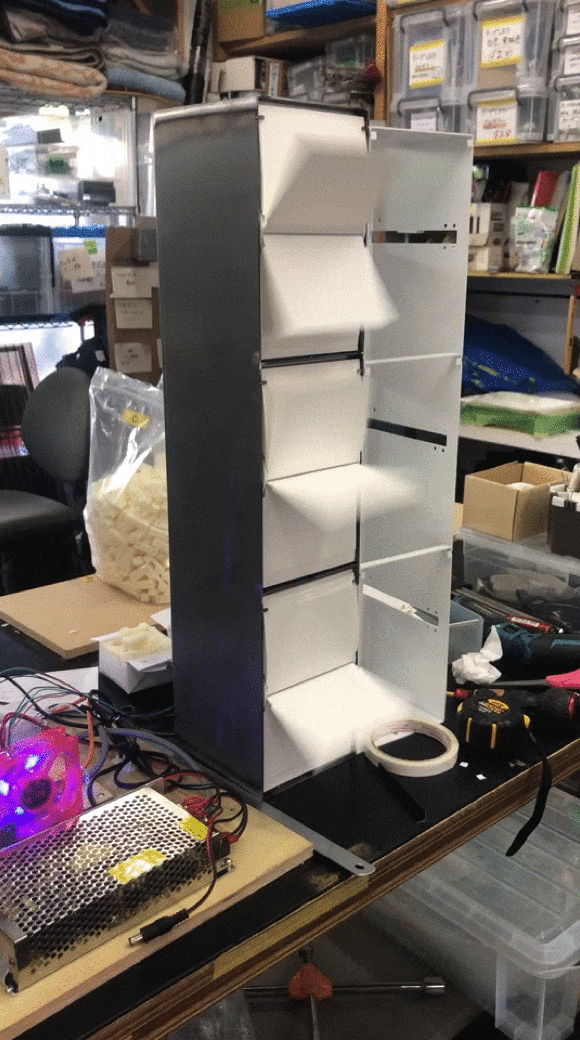
DMMへの発注で選んだ素材について
今回、ご発注いただいた素材はナイロンでしたが、ナイロンを選んだ理由はなんだったのでしょうか。
強度と表面の仕上がりです。
紙がめくれる際に隙間があくので、本体が少しだけ見えてしまう部分があるんです。
そのため素材の見た目がキレイで強度もあり、コストのバランスも良いナイロンを選択しました。
なるほど。
今回の制作物に、ナイロンの色味や物性がマッチしていたのですね。
そうですね、本当に少ししか見えないのですが、細部にまでこだわる必要がありました。
最初に何個か試してから本番用をご発注いただいたかと思いますが、実際の仕上がりはいかがでしたか?
最初に3個発注して仕上がりを確かめて、その後に100個依頼しました。
その後にちょっとしたトラブルがありましたが、おおむね大丈夫でした。
トラブルというと、どういった問題があったのでしょうか。
100個の造形依頼をした際、プリントの出力方向をこちらで指定していなかったので、穴の形状が少し潰れてしまっていました。
円柱を寝かせた形で出力いただいたのかと思いますが、DMMさんに相談させてもらって、結果的に再プリントしてもらえたので特に大きな問題にはなりませんでした。
なるほど。100個という膨大な数を効率良く造形するために、最初の3個と出力方向が違ったのかもしれません。
造形されたものは、今も展示されているのでしょうか。
展示期間が終わったので、会社で保管する形で置いてあります。
展示中も問題なかったので、大量に造形する必要があるような場合には今後も活用したいと思っています。
DMMを選んだきっかけや使ってみた感想
今回、DMMをお選びいただいた理由はなんだったのでしょうか。
見積もりがすごく早かったことが大きいですね。
他社と相見積もりしても金額が低かったので、DMMさんに発注しようかという決断になりました。
名前も普段から聞きますし、国内なのでサポート面の信頼性という理由もあります。
ありがとうございます。
最後に、DMM.makeのサービスを使っていて、良かった点や悪かった点があれば教えていただけますでしょうか。
悪かった点はそんなにパッとは思いつかないですね……。
サービス面ではおおむね満足しています。
ただ、出力方向を指定するサービスにお金がかかるなぁ……という印象でした(笑)
この辺をサービスしてもらえたら、かなり助かるなという感じです。
かしこまりました。出力方向の指定については社内で検討していけたらと思います。
それでは本日はこれにて終了とさせていただきます。
お時間いただきまして、ありがとうございました。
こちらこそありがとうございました。
株式会社TASKO
ホームページ https://tasko.jp/
インスタグラム https://www.instagram.com/tasko_inc/
Facebook https://www.facebook.com/taskoinc
Twitter https://twitter.com/tasko_jp