徳島大学 創成科学研究科 理工学専攻 機械科学コース 流体機械研究室の蓮岡颯太様よりお話を伺いました。つば付きディフューザー、いわゆる“集風体”のついた二重反転羽根車の性能評価を行っていらっしゃいます。風力発電用の小型風車の実験で、DMM.make 3Dプリントサービスの人気素材であるチタンを使った事例をご紹介します。
【蓮岡颯太様プロフィール】
平成11年生まれ
徳島大学 修士1年 (創成科学研究科 理工学専攻 機械科学コース 所属)
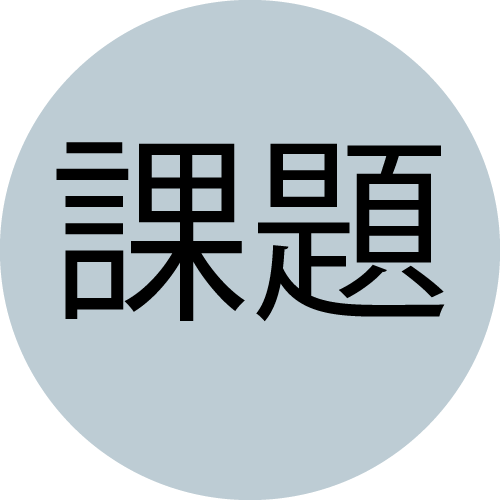
大学で使う実験装置は、再現が難しい形状・構造であるものが多々あり、その中には1年近くの期間を要するものもある。切削や金型など他のやり方では、形状・構造からコストがかかる上、納期が長い
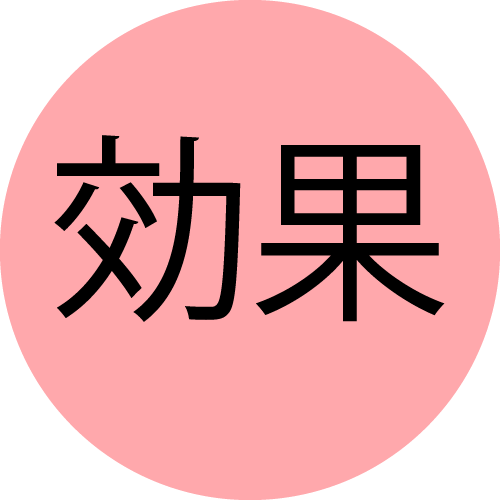
納期短縮
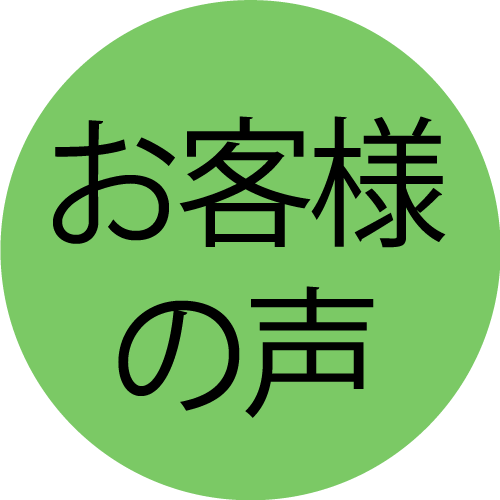
3Dプリントの発注から納品までは非常に早い
大学で取り組んでいる研究内容について
弊社の3Dプリントサービスをご利用いただきありがとうございます。
活用事例としてインタビューをさせていただきますので、よろしくお願いいたします。
よろしくお願いいたします。
早速ですが、蓮岡様の所属されている研究室と、そこで取り組まれている研究内容についてお聞かせいただけますでしょうか。
僕は徳島大学大学院、創成科学研究科の理工学専攻機械科学コースで、流体機械研究室に所属しています。
研究内容としては、つば付きディフューザー、いわゆる“集風体”のついた二重反転羽根車の性能評価を行っています。
▼ 二重反転羽根車の構造 ▼
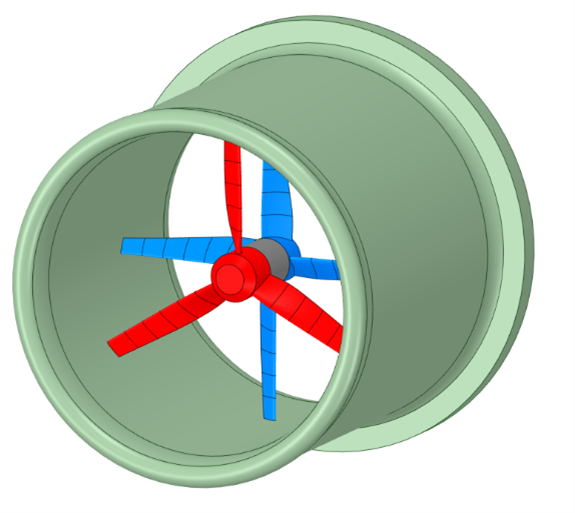
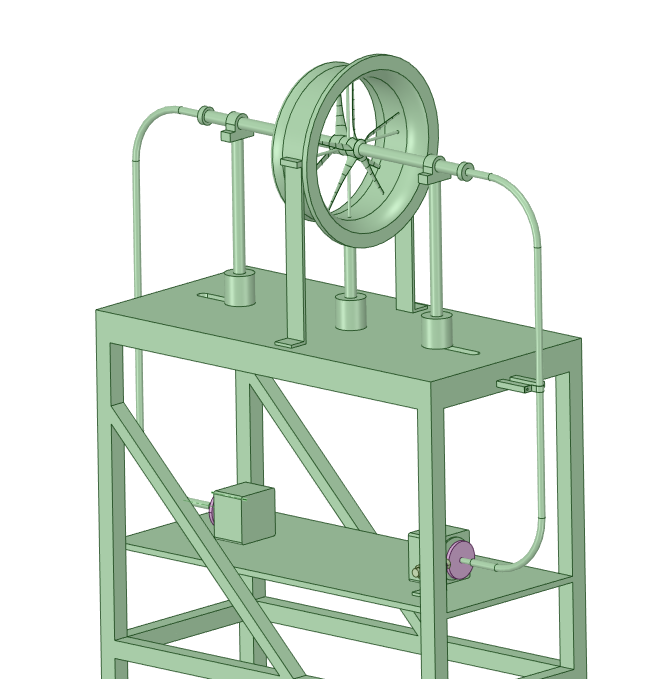
すみません、いろいろとわからない言葉が出てきました……(笑)
ゆっくりと伺いたいのですが、つば付きディフューザーというのはどういったものでしょうか。
「風車」と聞くと、一般的には3本の羽がついていて、何も付いていない柱が立っているだけの風車を想像されるかと思います。
これを「プロペラ風車」と呼ぶのですが、僕たちは羽の先端の周りに筒状のものを取り付けて、その中に風車を置くようなデザインになっています。
風をより効率良く集めて、内部に風を流すことができれば、もっと上手く風車を回せるという発想で、つば付きディフューザーを取り付けた風車の研究に取り組んでいます。
なるほど。
蓮岡様が研究されている風車は、一般的なものよりも新しい形式なのでしょうか。
用途によってはすでに使われているかもしれません。
有名な洋上風車になると、そもそもの大きさがとてつもなく巨大なので、集風体を取り付けるのが非常に大変なのです。
僕らの研究内容でいえば、風力発電用の小型風車でそこまで大きくないという理由から、つば付きディフューザーを付けて実験を行っています。
研究室で開発したものは、すでに実用化されているのでしょうか。
現状では実用化されていません。
僕らの研究は、一昨年くらいから準備が始まったくらいの最近のものになります。
基本的に要素研究といって、モデル実験や解析を繰り返し行って、どうやって性能を上げていこうかと試行錯誤しています。
製品開発の実験モデルではないので、基礎研究のようなことをずっと繰り返し行っているイメージです。
いろいろなパターンや形を試しながら、どういうものが効率良く発電できるのか、風を集められるのかを実験している状態ということですね。
3Dプリンターで造形した「羽根車」の活用方法について
小型の風車を作るとき、3D CGなどを使ってシミュレーションを行うかと思います。
その中で、今回3Dプリントしたものはどのように活用されているのでしょうか。
検証用の実験機に取り付ける羽根車として活用しています。
モデル実験として使うためのものなので、実物よりも小型のサイズで造形をお願いしました。
大学の中に風力を試験できるような環境があるのでしょうか。
はい。大学の中に風を送るための機械があるので、それを使って検証しています。
今回は3Dプリントをご依頼いただきましたが、それ以外の手法でプロペラの造形や加工を行った経験はございますか?
僕の研究はまだ日が浅いので、現時点ではそこまで大掛かりな方法を試したことがありません。
また、前に取り組まれた研究はかなり昔のことだったので、当時どういった方法で造形していたかは、正確にお答えできない部分があります。
とはいえ、風車のなかでもクロスフローという特殊な形状のものを使っており、恐らく切削と組み立てで作られていたと思います。
※クロスフロー:風車の水平軸風車と垂直軸風車に大別され、クロスフロー風車は垂直軸風車の一種。
3Dプリンターで風車を造形すること自体が初めてだったのでしょうか。
そうですね。
ただ、研究室内の他の研究で3Dプリンターを使っているものがあったので、それを参考にした部分はあります。
具体的にどういったものを参考にしたのでしょうか。
船舶のスラスターです。船の下についているプロペラみたいなものですね。
あれのモデル実験などで3Dプリンターを使っていたという話を聞いて、もしかしたら風車も3Dプリンターでいけるのではないかと思ったんです。
なるほど。
ちなみに、大学内に3Dプリンターは設置されているのでしょうか。
大学内にはありません。
大学の工場にあるのは、切削機械などの一般的なものがほとんどです。
3Dプリントで造形する機械は、僕が知る限りでは存在しないかと思います。
大学内で実験器具を作る場所は、学生さんも自由に使えるのでしょうか。
使えます。
自分で加工するときもあれば、精度が必要な場合は技官さんに依頼するパターンもあります。
なるほど、すごいですね。
実際に形を作るだけで終わりではなくて、自分たちで工夫しながら検証しないといけないのはかなり大変そうですね。
そうですね。技術的にできないこともありますが、そういう場合は「実験で何を知りたいのか」に焦点を当てています。
風力発電用の風車で言えば、発電効率は度外視で検証用として回転数だけ分かればいい、などです。
そういうところに焦点を当ててあげると、何を優先すべきかが見えてくるので、そういう形で技術的な部分と照らし合わせながら検証を行うようにしています。
DMM.makeを選んだきっかけと、チタンを使った理由
DMM.makeを選んだきっかけを教えてください。
3Dプリンターを使おうと思ったときに、何社かに問い合わせをして相見積を出してもらいました。ただ、今回のような形で試作するのが初めてだったので、そもそも他の会社を見つけるのが大変だったんです。
その中でもDMMさんは国内でも大手ですし、すぐに見つけられたというのが大きな理由になりました。
なるほど。
研究室として3Dプリントを頼む経験が珍しいので、そもそもどういう業者がいるのか調べることが難しかったのですね。
3Dデータの入稿も蓮岡様が進めていたのでしょうか。
先輩が基本の3Dモデルを作っているのですが、データの入稿などは僕もやっていました。
実際に取り組んでみて、難しいと感じたポイントはありましたか?
特に難しいと感じる部分はありませんでした。
画面を見ながら操作すれば、簡単にデータの入稿ができたので助かりました。
素材としてチタンを選んだ理由について、教えていただけますか?
強度が欲しかったので、金属で造形しようと考えていました。
ただ、風車は軸で支えるものなので、重すぎると軸が曲がってしまうなどの問題が出てしまいます。
なので「軽量かつ強度があって壊れないもの」という理由からチタンを選ばせていただきました。
風車が回転する軸と、風車そのものの軸の2種類があるかと思いますが、軸で支えるというのはどの部分でしょうか。
風車そのものの軸の部分に関しては、強度を優先しました。
基本的に、軸の部分はベアリングなどで下から直接支えることができるので、そこまで軽量化にこだわる必要はないという判断です。
一方で、羽根車の部分はそのものが回転するので直接支えることができません。
羽根車が軽くないと、軸の部分がたわんできてしまう可能性があったので、強度もありつつ軽量であるチタンを選びました。
金属の中では軽いことから、チタンが選ばれたのですね。
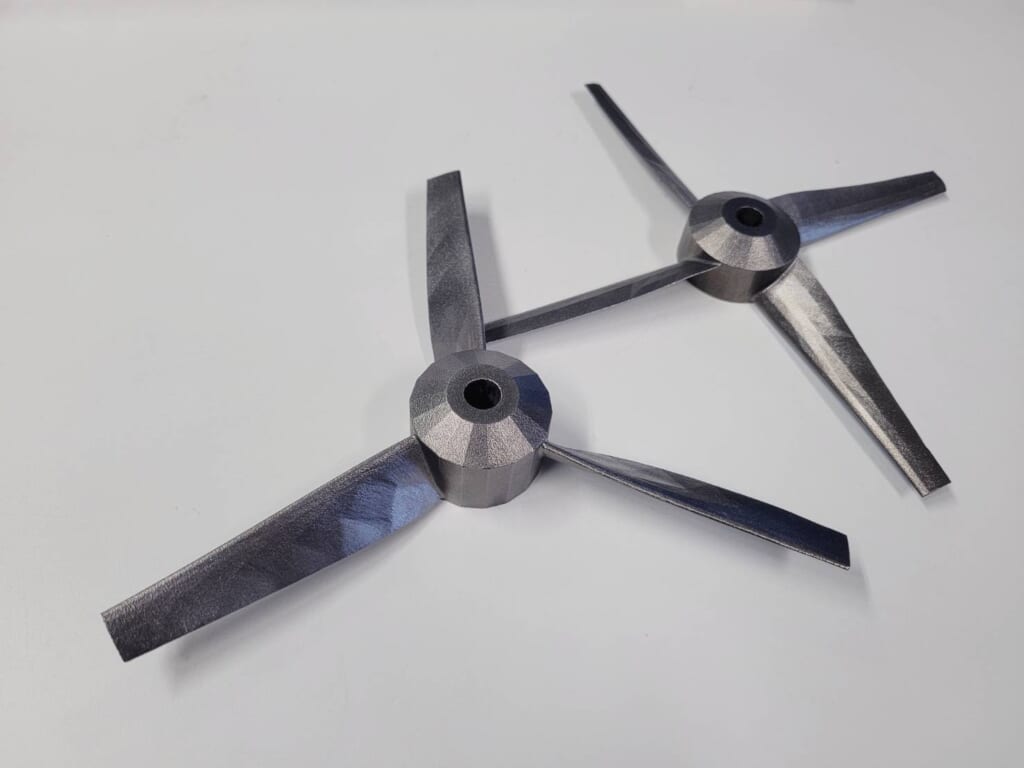
プロペラの設計に使うCADと実験手法
3Dモデル自体も作っているということですが、どういうCADソフトを使っていらっしゃるのでしょうか。
「Ansys(アンシス)」の「SpaceClaim(スペースクレイム)」です。
CFD(Computational Fluid Dynamics, 数値流体力学)などをやるときに使うAnsysの中に、3DモデリングができるSpaceClaimがあったのでそれを使っています。
*編集部注釈:2022年7月にSpaceClaim Engineerは販売を終了しており、後継製品は、Ansys Discovery Modelingです。
3Dデータのモデリングから実験の解析までは、一気通貫で取り組めるのでしょうか。
恐らく、Ansysを使えば一通りはできるかと思います。
設計の数値などの細かい部分は、別でエクセルシートを使って管理しています。
その数値さえ決まってしまえば、その数値から3Dモデルを起こして、設計と組み合わせて……という感じで進められますね。
蓮岡様は、大学の授業などで設計や3Dモデル制作に親しみがあったのでしょうか。それとも、研究内容に合わせて独自に学ばれたのでしょうか。
学部の授業では、少し触れたことがある程度です。
学部生の頃は別の研究室でしたが、大学院で今の研究室に移ってからはCADをバリバリ使うので、その中で身に付けていきました。
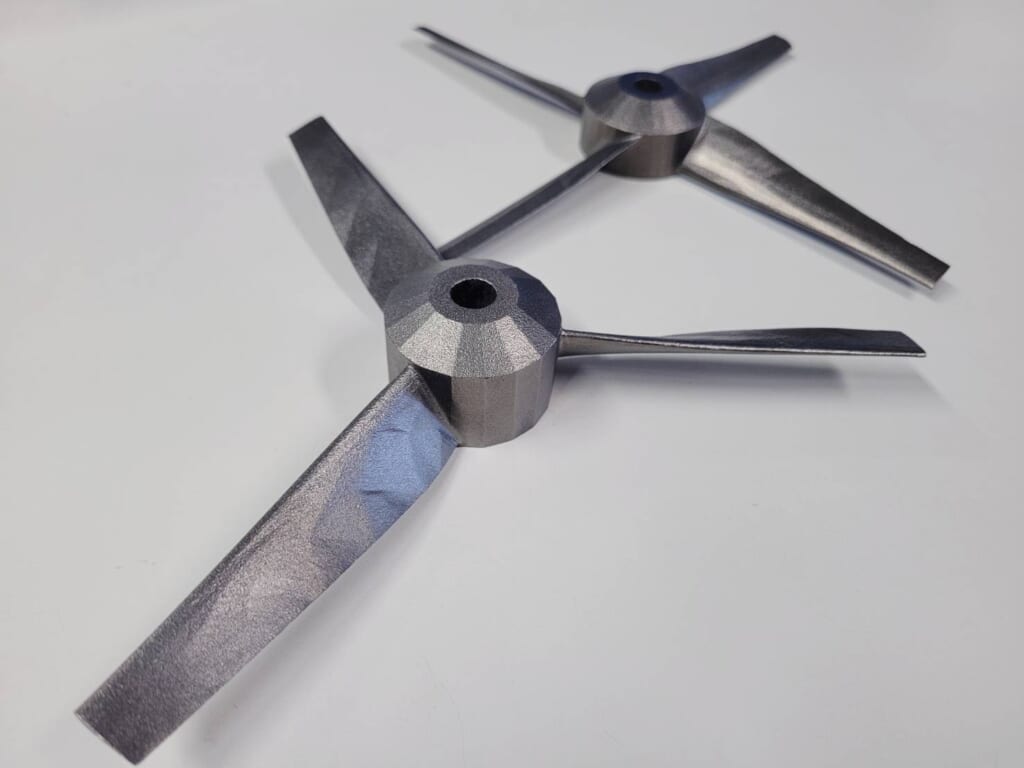
プロペラの造形はとても特殊で、難しそうに感じます。
そのデータを作る方法は、研究室の中で叩き込まれるのでしょうか。
そうですね。ただ、羽の造形の部分はCADなどでそのまま作れるわけではないんです。
まずはエクセルで数値を出して、その数値を読み込んでから羽を造形するので、一般的な3Dプリントとは違って、かなり特殊な作り方になると思います。
ベストな数値を探すのも、研究の中でひとつのトピックになりそうですね。
そうですね。
研究を始める際は、基本的に他の大学の先行研究や小型風車の製品などを参考にしてモデルを作っています。
参考にしたモデルから少しずつ数値をずらしていくと、性能曲線だとか効率だとか、それらの頂点と下がってくる箇所が分かれてくるので、そういった情報を参照しながらどのモデルがいいかを検証しています。
実際に造形したものは、何十個もあるパターンの中から、一番いいと思われる数値で制作したのでしょうか。
はい。今回の実験を含む要素研究のモデル実験というのは「妥当性」を示すものになります。
今までの研究解析のパラメータの中で最適だと思って出した数値、これがどれくらい当てはまっているのか、その妥当性を知るために実験しています。
3Dプリントする際にも、これまでのパラメータの中で、最適だと思われるものを選出して造形しました。
実験結果によって、パラメータを変えたり、他の部分をいじったり、繰り返し作り変えていくようなイメージでしょうか。
作り変えることはほとんどありません。
一個一個を作り変えるのではなくて、今回のように半分が終わったら、最後の半分をまたやって、最終的な段階で結果を見るようなイメージです。
妥当性を示すというのは、解析と実験モデルがどれくらい合っているか示し合わせるものなので、簡単にいえば「解析の信憑性を上げたい」という感じですね。
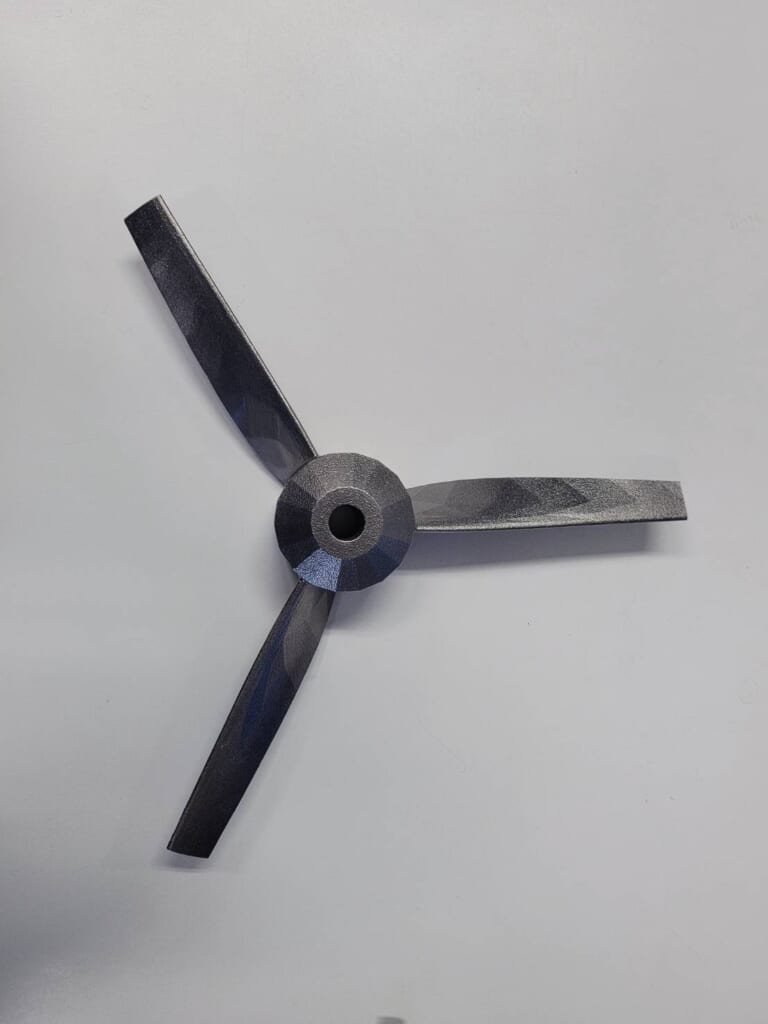
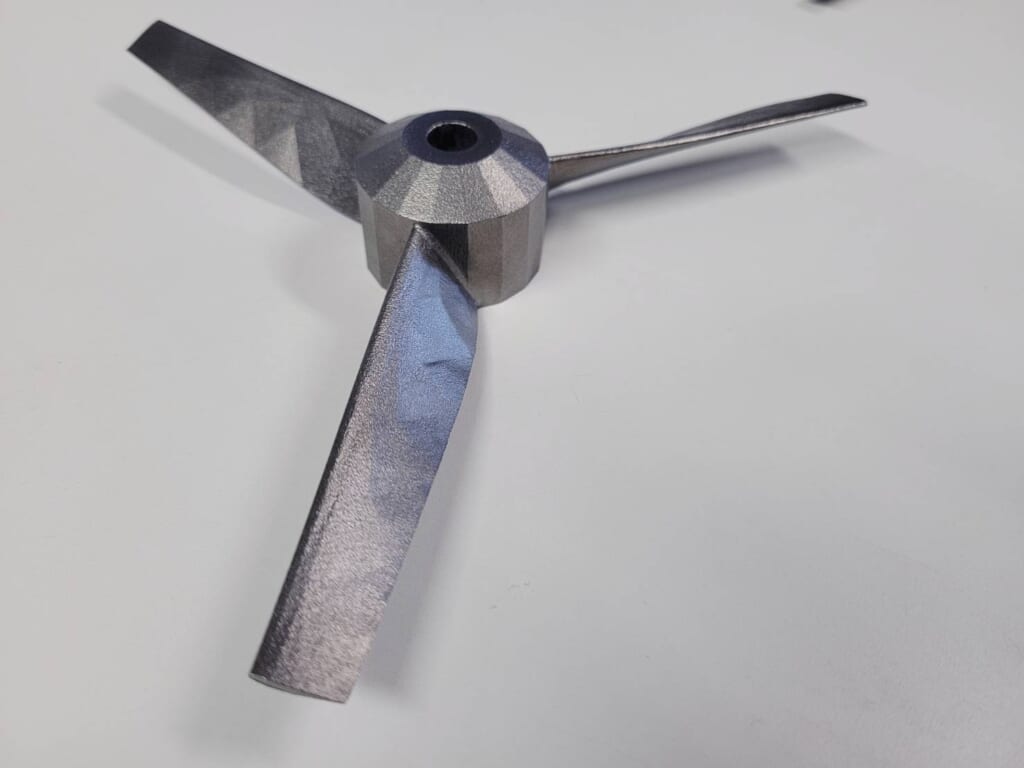
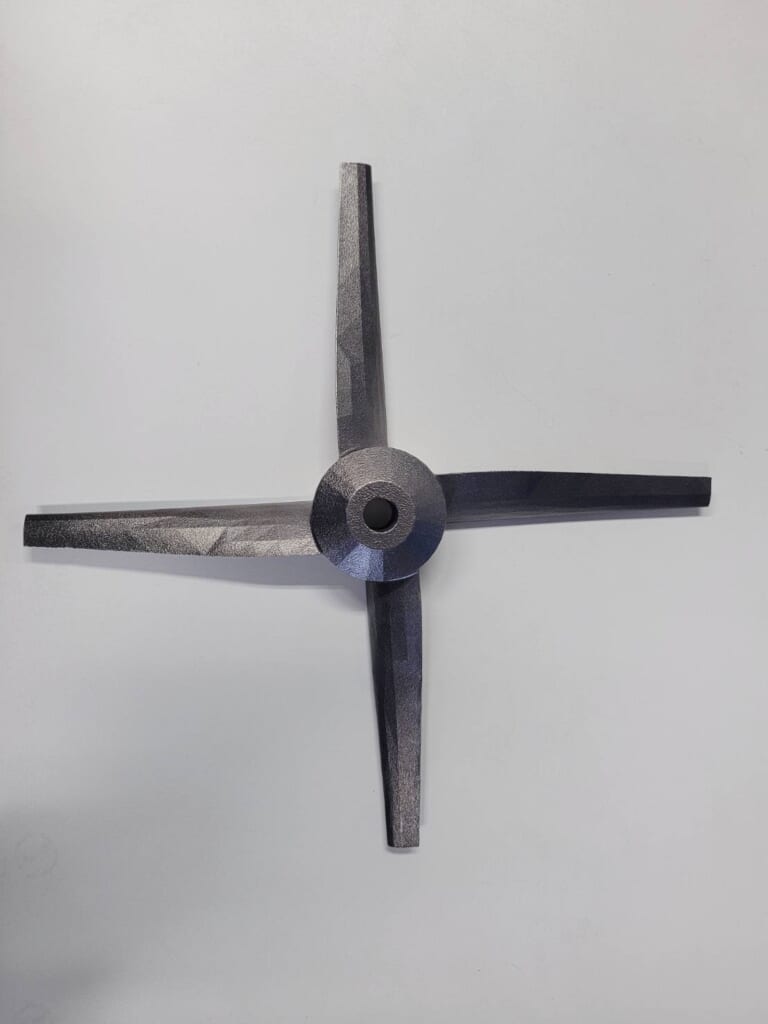
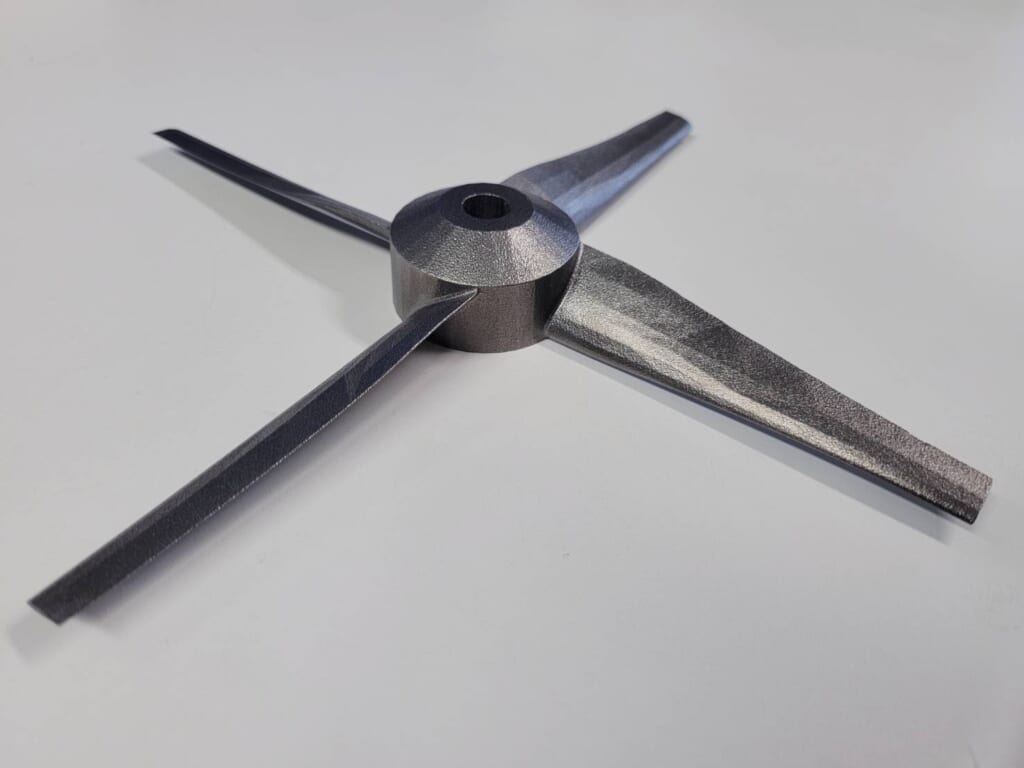
造形物の仕上がりと納品スピードについて
3Dプリントした造形物の仕上がりはいかがでしたか?
熱応力などの歪みで、羽それぞれの角度が違っているなどの問題がありました。
これについては一度、DMMさんのほうで造形し直していただく形で依頼させてもらいました。
修正したものは実際の実験にお使いいただいたのでしょうか。
まだ組み上がっていないので、実験としてはこれからになります。
今は最初に出したモデルを修正して、これから実験を行うということですね。
造形に出す時点で、熱応力の歪みは想定されていたのでしょうか。
想定はしていませんでした。
船舶のスラスターで上手くいった理由と、風車で上手くいかなかった理由を照らし合わせた結果、風車の長さが原因なのかなと思っています。
羽の部分が長くなってしまうのと、薄さの問題があるのかなと。
なるほど。
造形のときにちょっとした変化が起こり得ると。
はい。長ければ長くなるほど、少しの変形の影響が大きくなってしまうんです。
たとえば、根本で1mmのズレがあると、羽の先端に行くにつれてそのズレがどんどん大きくなって、最終的に1cmもズレてしまう、といった具合です。
根本からの変形が少しずつ積み重なってしまうので、長さの影響が一番大きかったのかなと思いました。
歪みを想定したモデルを作る、というのが素人目線での改善策かと思いましたが、その点はいかがでしょうか。
歪みを想定しようとすると、実際の歪みがどうなるかを計算しないといけません。
どの程度の変化があるのかは未知数なので、歪みを想定してモデルを作るのは難しいかなと思います。
取れそうな対策としては、歪みそうな部分を厚くしてあげるとか、あえて補助の柱の部分を付けて、最後の切削でそれを削るなどが考えられそうです。
ただ、僕自身、そこまで3Dプリンターに詳しいわけではないので、何ともいえないのが現状です。
弊社としても、こういったものを依頼されることは多くないので、今後対応できる幅を増やしていければと感じました。
ちなみに、注文してから実際に届くまでのスピード感はいかがでしたか?
どちらかといえば早いなという感想です。これまで加工や製造を発注すると、普通は1〜3ヶ月くらいの時間がかかっていました。
去年の研究室では、1年かかっても依頼したアイテムが届かないことがあって、検証前に先輩が卒業してしまう事件もありました(笑)
それらと比べると、3Dプリントの発注から納品までは非常に早いなという印象があります。
実際の期間としては、どれくらいで届きましたか?
数ヶ月前のことなので、具体的にはあまり覚えていません。
2〜3週間くらいで、1ヶ月はかかっていなかったかと思います。
なるほど、ありがとうございました。
それではお時間となりましたので、今回はこれにて以上とさせていただきます。
貴重なお話、誠にありがとうございました。
ありがとうございました。
徳島大学 創成科学研究科 理工学専攻 機械科学コース 流体機械研究室 ホームページ
https://www.tokushima-u.ac.jp/st/graduate_school/course/machine_science/