DMM.makeの3Dプリントサービスをお使いのお客様の事例を紹介する本連載。今回は、ご自身でデザイン事務所を経営し、試作などに3Dプリントを活用しているARUPaPa様をご紹介します。
プロダクトデザインに3Dプリンターを活用
本日はよろしくお願いいたします。
さっそくですが、3Dプリンターで何を作っているのかご説明いただけますでしょうか。
私はデザイン事務所をやっていまして、基本的にはメーカーさんなどから仕事を受託しています。
主にボトルなどの工業製品を手掛けていますが、最近では医療機器関連のお仕事にも携わっています。また、私が住む地域の中小企業さんのお手伝いも積極的に行っています。
3Dプリントを始めたきっかけは、ご自身でプロダクトデザインをする際に必要となったからでしょうか。
そうですね。私は30年くらい前にメーカーに就職してデザイン業務を担当していました。当時から業務用の3Dプリンター自体は存在していました。とはいえ、そのメーカーとして3Dプリンターを導入することはなく、アウトソーシングで造形していました。光造形のとても高い機種を入れているモデル屋さんがあって、そこに依頼したりしていましたね。
30年くらい前は3Dプリントという名称ではなく、ラピッドプロトタイピングといった名称でしたよね。独立してから、ご自身でも3Dプリンターを導入したのでしょうか。
自分の事務所に導入したのは7年前くらいのことで、FDM方式の3Dプリンターを自分で組み立てるところから始めました。当初はなかなかうまく造形できず使いづらいと思っていましたが、次第に慣れてきて、今まで手で作っていたものを3Dプリンターに置き換えられるようになってきました。
事務所で使われている3Dプリンターは、どのような機種でしょうか。
最初に使っていたのは、ボンサイラボさんが監修した「idbox!」です。2015年にデアゴスティーニから刊行されていた「週刊マイ3Dプリンター」に付属していたもので、トータルで10万円ちょっとかかりましたが、組み立てながら構造を勉強しました。
しばらくの間は問題なく使えていたのですが、造形サイズがあまり大きくなかったので、ネット通販で5万円くらいの機種に買い替えました。今は300×300×400mmくらいの造形サイズで、2リットルくらいのボトルを造形できるものを使っています。
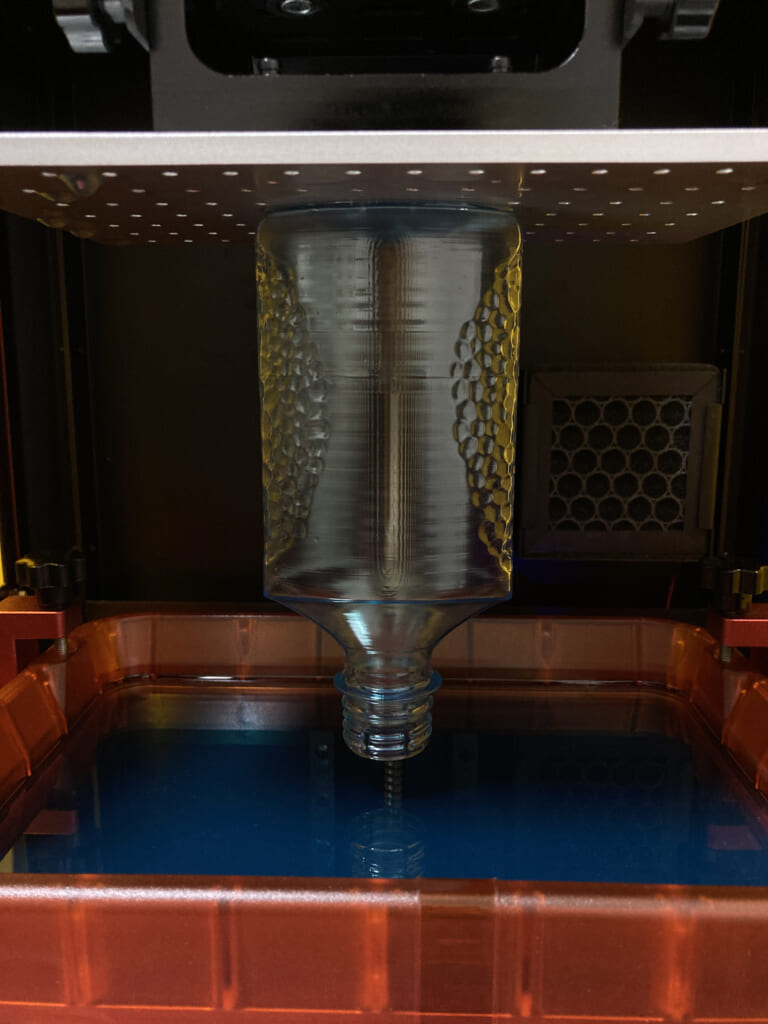
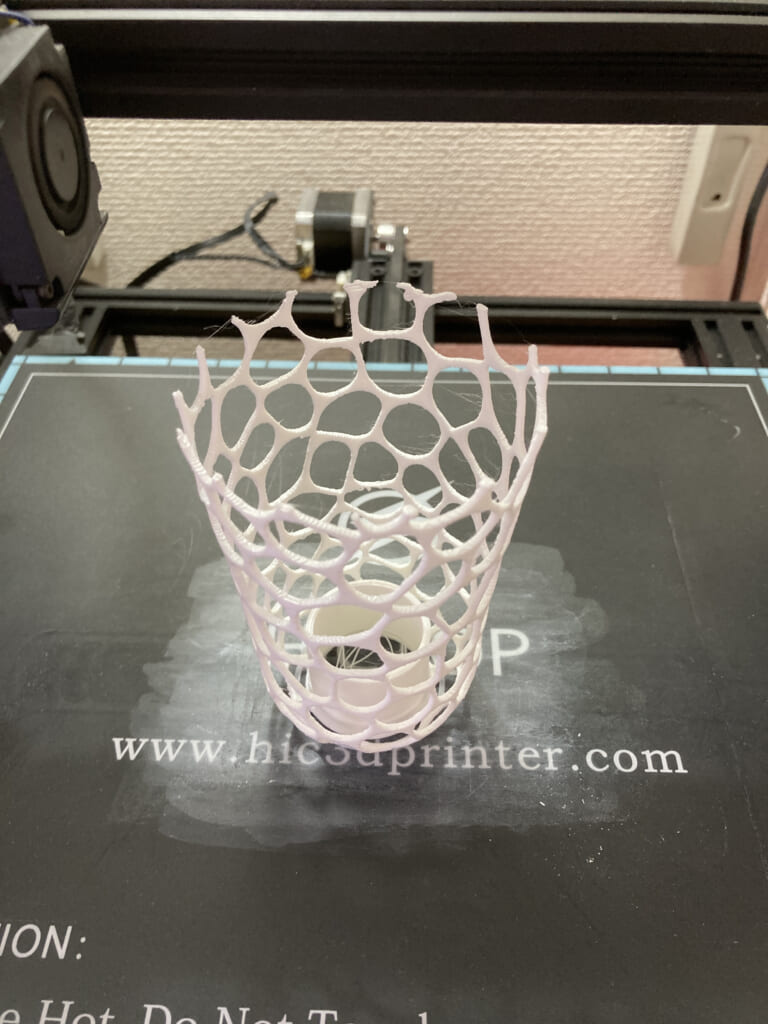
3Dプリンターをご自身の業務に導入してみて、いかがでしたか?
以前は「スタイロフォーム」という青い発泡材をヒートカッターで大まかに切って、サンドペーパーで形を整えて、実際に自分の手で握ったりしながら造形していました。ただ、そういう手順を踏むと、発泡材の粉が出てしまうので、作業する環境がとても悪くなってしまいます。
3Dプリンターを使い始めてからは、そういう作業がほとんど無くなり、作業環境がかなり改善されたので、非常に良かったと感じます。また、3Dプリンターで造形している最中に別の仕事にも取りかかれるので、非常に便利なツールだと思っています。
業務に合わせてCADも変える
これまでどのようなCADを使ってきましたか?
メーカーにいた頃は「I-DEAS」(現在の「NX」)というソリッド系のCADを使っていました。レンダリングはWavefrontです。
メーカーとして、CADなどを使ってお仕事されていたんですね。
当時は住宅設備の会社にいたので、システムキッチンや浴槽などのデザインをしていました。
今使っているCADについても教えてください。
「Rhinoceros」と「SOLIDWORKS」を使っています。
SOLIDWORKSはプロ用のライセンスを入れていますが、初期費用に100万円くらいかかりました。それに加えて保守料もかかるので、なかなかコスト面は高いなと感じています。
Rhinocerosを導入した理由はなんだったのでしょうか。
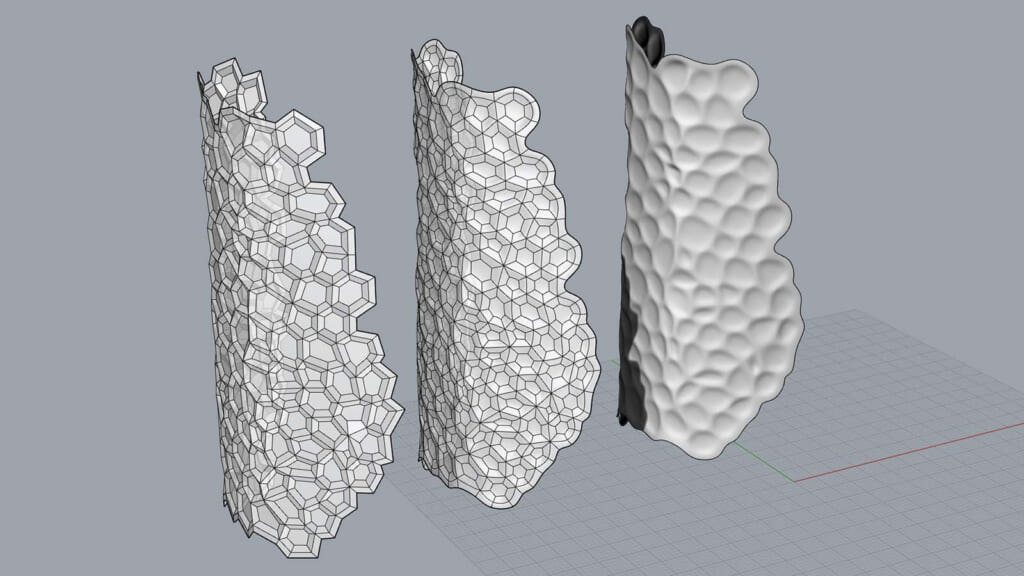
ボトルのモデリングで使うためです。大手の容器メーカーさんから仕事を受けているときに、メーカーのデザイン部門がRhinocerosを使っていました。有機的な曲面のサーフェスを貼る仕事が増えてきたので、ネイティブデータでの納品ができるように、同じソフトを導入しました。それからRhinocerosは長いこと使い続けています。
素材の特性を活かしたものづくり
個人で取り組んでいるプロジェクトについても伺いたいのですが、展示会に出したものはどのように作っているのでしょうか。
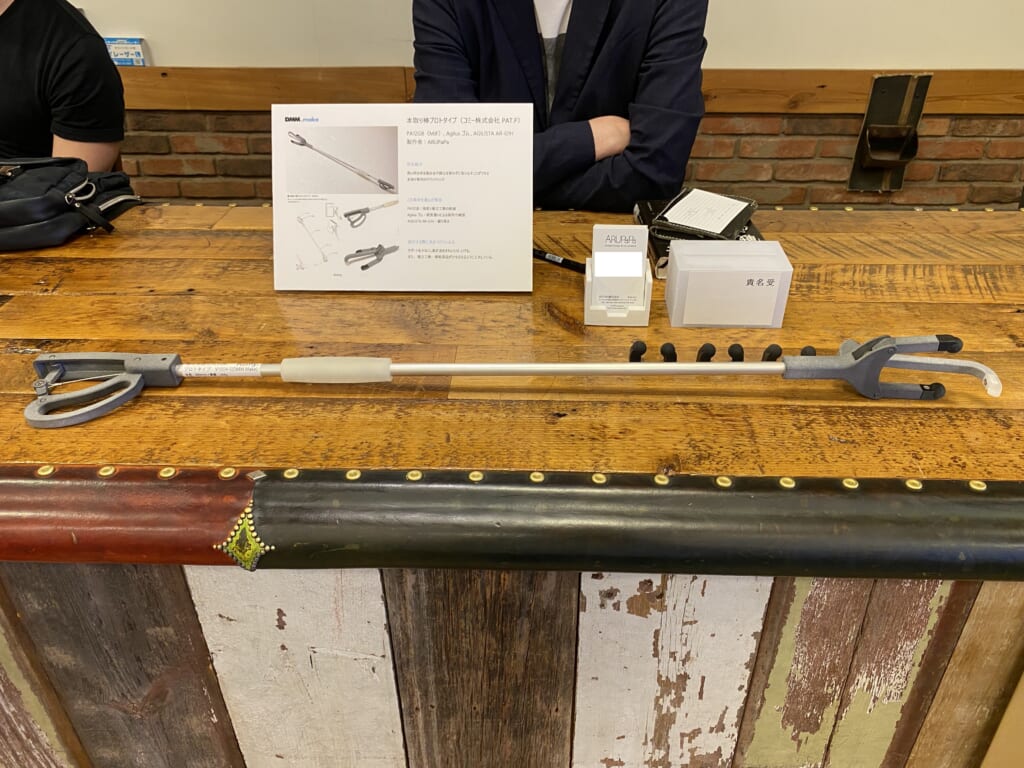
機構ものなので、ラフスケッチから始めて大まかなイメージを検討します。その後、CADを使ってざっくりとモデリングして、3Dプリンターで出力して大まかな動きを確認しています。その工程をだいたい5回くらい繰り返すと、イメージしたものに近い造形物ができあがります。
強度が必要な機構部品には、MJF(マルチジェットフュージョン)も使っていただいていますが、実際に造形してみていかがでしたか?
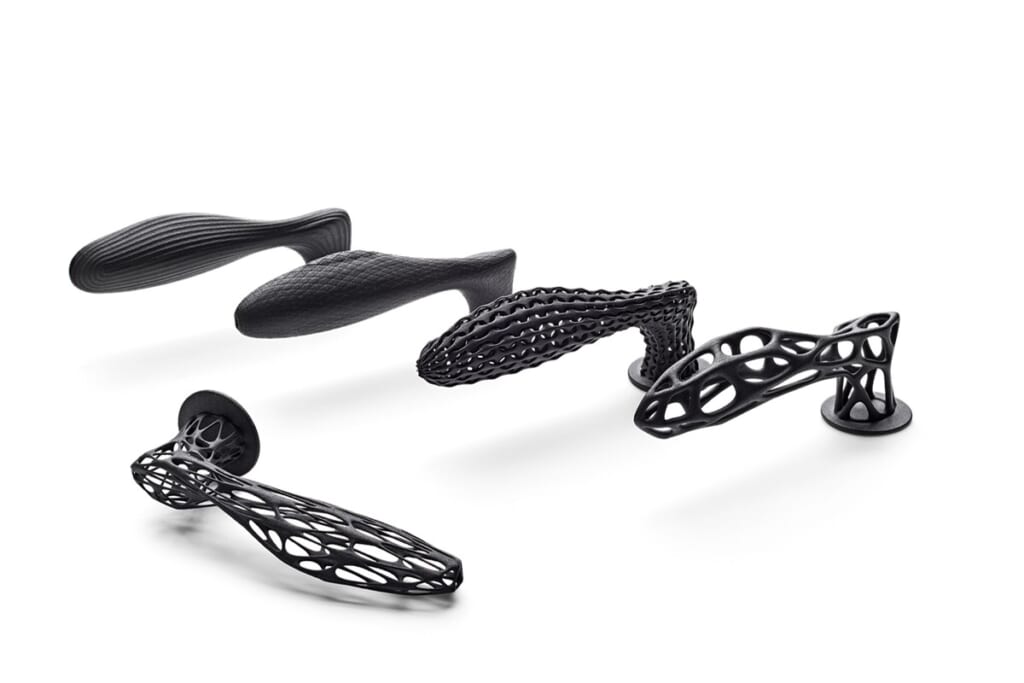
組み立ての際に締結部品を使うと、ねじが多くあったりして、組み立ての工数が増えてしまいます。そこで今回は、曲がる部分や複数のパーツがジョイントされている部分をMJFの一体造形で出力して、最低限の締結部品で取り付けられるような試みをしました。
既製品だと複数パーツに分かれてしまう部分を、ひとつにまとめるイメージで造形したのですね。
そうですね。サポート材を後から外す必要もないので、他の箇所や部品でもいろいろと使えそうだと思いました。
Agilusゴムも使っていただいています。弊社でも事例が多くないのですが、使用感はいかがでしたか?
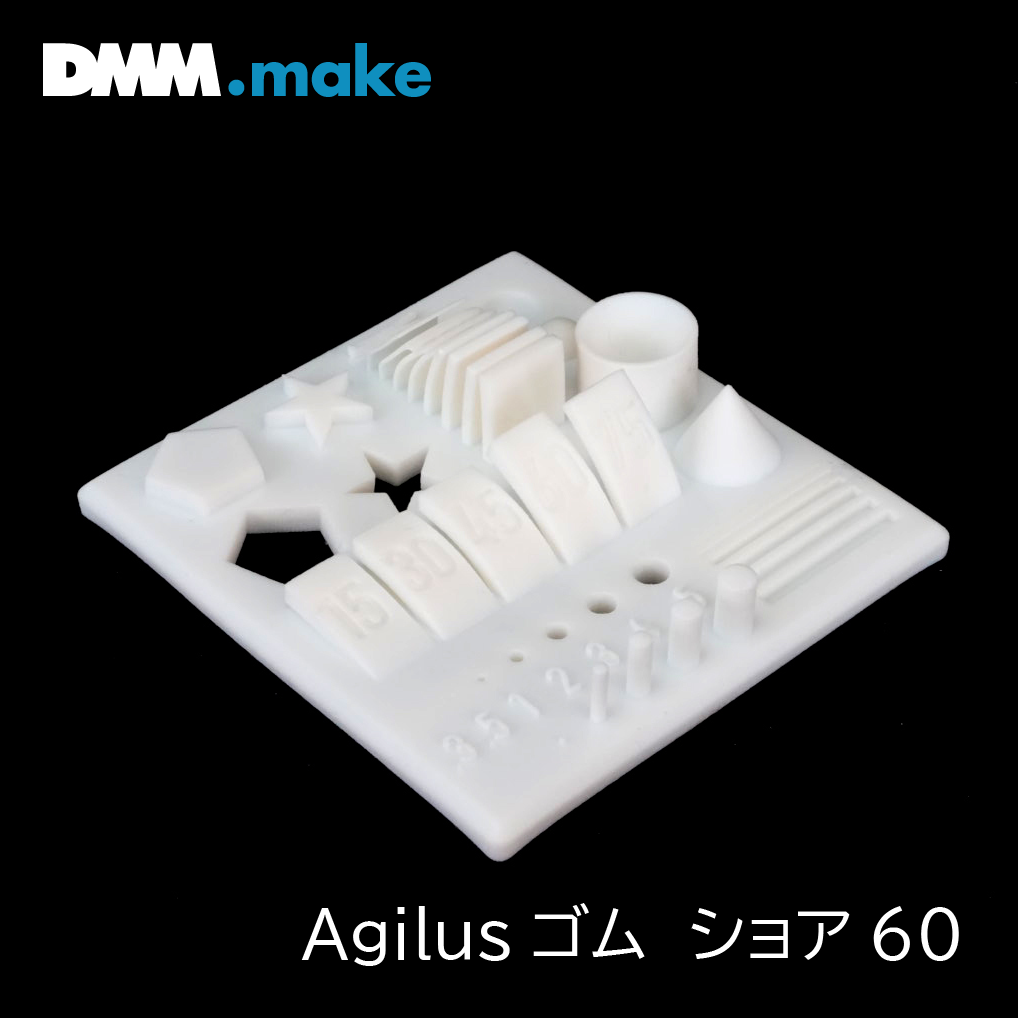
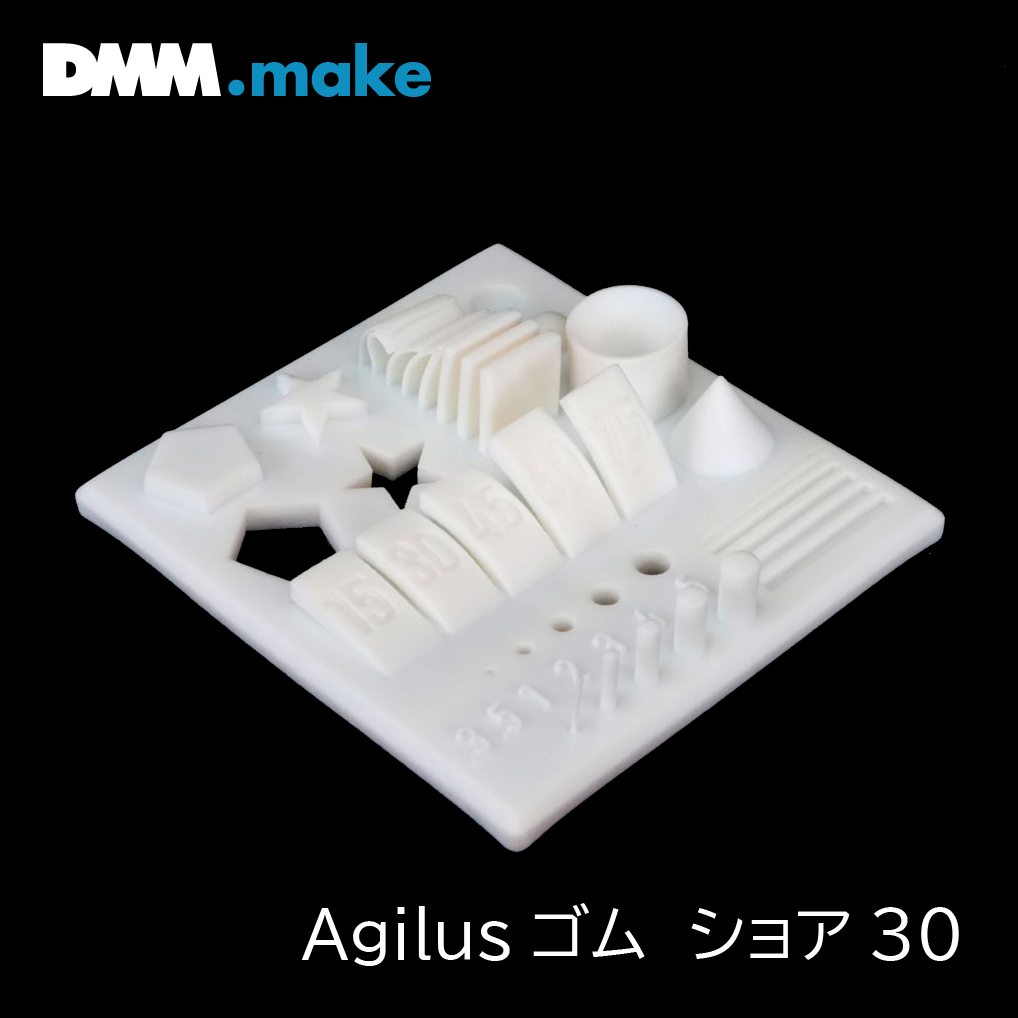
高いところにある本を掴むためのものを作ったのですが、その先端部分にAgilusゴムを使ってみました。先端が硬いと掴んだものが滑ってしまうので、人間の指と同じくらい柔らかいもので造形する必要がありました。
硬度を変えられる素材が他になかなかないので、Agilusゴムの硬度を変えて4パターンほど実験的に作ってみました。実際に取り付けて、どれくらいの柔らかさがよいのか検証を行いながら、ベストなものを選んでいきました。
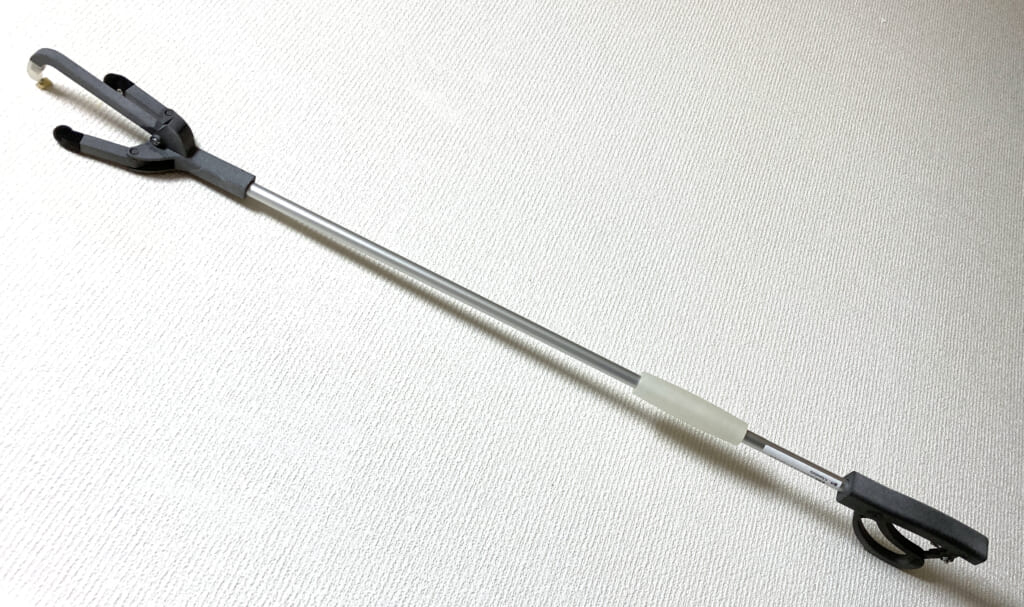
他の素材はどのように使っていますか?
表面を滑らかにしたい部分や、強度もきちんと検討したい場合には、ナイロンの粉末を使って造形しています。
形を見るだけであれば、FDM方式の3Dプリンターで出力するだけでも済みます。事務所にある光造形方式の3Dプリンターで作ることもありますね。
私生活でも使える3Dプリンター
3Dプリンターを使っていてよかったと感じることはありますか?
ものが少ない戦後の頃には、私の父親なんかは大工道具を持っていて、欲しいものがあれば木を切ったりして、すべて自分で作っていました。
今はものが溢れていて、探せばなんでも買える時代になりました。そんな中で登場した3Dプリンターは、「自分が欲しいものを作るための新しいツール」という価値観を生んだと思っています。
なるほど。
最近はDIYが流行っていますが、自分が生活する上で必要なものを簡単に造形できるようになったのは、今だからこそできるニーズというか文化というか、新しい時代だなと感じます。
普段の生活の中で「これ、もう少し短ければいいのに」とか「こうしたら付くのに」とか、そういった細かい要望ってたくさんあるじゃないですか。私自身も仕事以外に、ちょっとこういうものが欲しいなと思ったり、日用品の壊れた部品の補修などはパパっとモデリングして3Dプリンターで造形して、家の中や車で使ったりしています。
自宅に3Dプリンターが1台あると、そういうことができて楽しいですよね。大量生産・大量消費の時代から、自分が欲しいものを自分で作る「ものづくりの時代」になってきているということですね。
そうですね。あとは既製品に付け足して使う方法もありますよね。100円ショップで売っているようなものに、3Dプリンターで作った部品を取り付けたら、まったく違う価値が生まれることもありますし。
今回の展示会で知り合った出展者は、キーボードやプラモデルを作っているような人たちがいて、副業として商売できているのですごいなと感じています。
DMM.make 3Dプリントの長所と改善点
DMM.makeはいつ頃からご利用いただいているのでしょうか。
2015年8月くらいに会員になったかと思います。普段はFDM方式の3Dプリンターをかなりの頻度で使っているのですが、当時は光造形機を持っていなかったので、透明な材料で出してみたいと思って登録しました。
業務で透明な素材が必要だったのでしょうか。
当時はRhinocerosを使ったボトルの3Dモデリング方法をブログで連載していました。モデリングして終わりではなく、造形の仕上がりまで見せるために、3Dプリンターを利用した次第です。
DMM.make以外の他社サービスを使ったことはありますか?
納期の関係でとても急がなくてはいけないときは、短納期対応が可能な他のサービスを使っています。
なるほど。それでもDMM.makeを使い続けている理由について教えていただけますか?
やはりコストの面が大きいですね。多少の納期がかかっても、コストを優先したいときにはDMMさんを使わせてもらっています。材料をたくさん揃えているところも、他社にはない魅力のひとつだと思います。
また、量産の目処が立っていないような中ロットや極小ロットのものは、金型を起こさずに3Dプリンターで造形して、そのまま製品にしようという試みがあります。私のクライアントも、数が出ないものでは金型を起こさず、MJFで造形したものをそのまま製品として販売しています。
特殊な形状の部分を作る際は、金型だと数百万円のコストがかかってしまうので、3Dプリンターを活用するモノづくりは、BtoBの製品でどんどん広がっていくと思います。
逆に、DMM.makeのサービスを使っていて、大変だったことはありますか?
最初は造形の依頼をするときに、パーツごとに組み合わさった状態でデータをアップロードしていました。そういう状態で造形してほしいという意味で組み合わせていたのですが、システムで自動的にレイアウトを配置したせいか、すべてバラバラで届いてしまいました。ガイドライン通りにデータを作っても、イメージ通りの造形がなかなかできないので、その点は難しいと感じました。
すこし難しいですよね。造形するスタッフの解釈が入るといいますか……。データをアップロードする画面などに備考欄があれば、より注文しやすいでしょうか?
そうですね。チェックボックスが一個あるといいかなと思います。データの通りに造形してくださいとか、バラバラになってもOKですよ、とか。
参考にさせていただきます。
今後取り組んでみたいこと
今後、取り組んでみたいことがあれば教えてください。
金属の造形ですね。自分で発信するプロダクトに金属素材を使えたらいいなと考えていて、特にチタンにはチャレンジしてみたいと思っています。
金属のプロダクトを作ってみたいのですね! 具体的な案はすでにあるのでしょうか。
今はまだありませんが、今後アイデアと結びついたときにやってみたいと考えています。
最近はナチュラルな表現というところで、自然のテクスチャーをいかに再現するかという流れが強いと感じています。CGの世界で自然なテクスチャーを再現するのは得意ですが、それをCADで起こすのはなかなか難しいので、試行錯誤している最中です。
最後に、なにか宣伝したいことがあれば教えてください。
最近、おもしろいものを作りました。「セルオートマトン」という数理理論があるのですが、それを立体にしたらどうなるか考えて、3Dのモデルを自分で作りました。
それを東京大学の先端科学技術研究センターで渋滞学を研究している西成先生のところに持っていったら大変喜んでいただきました。こういう「研究で使う理論」を立体にして、体験できる仕組みが作れたら面白いと思います。
ありがとうございました。
ARUPaPa様 ホームページ http://www.arupapa.jp/