「自分が注文した3Dデータを作っているのはどんな人なんだろう」と思ったことのある方はいらっしゃいませんか。
以前に加賀工場のご紹介をしましたが、この記事では加賀工場で働く”中の人”の声を座談会形式でお届けします。
今回は造形担当の小山、東口、前田に一日の仕事の流れ、仕事のやりがい、今後の仕事への意気込みなどを語ってもらいました。
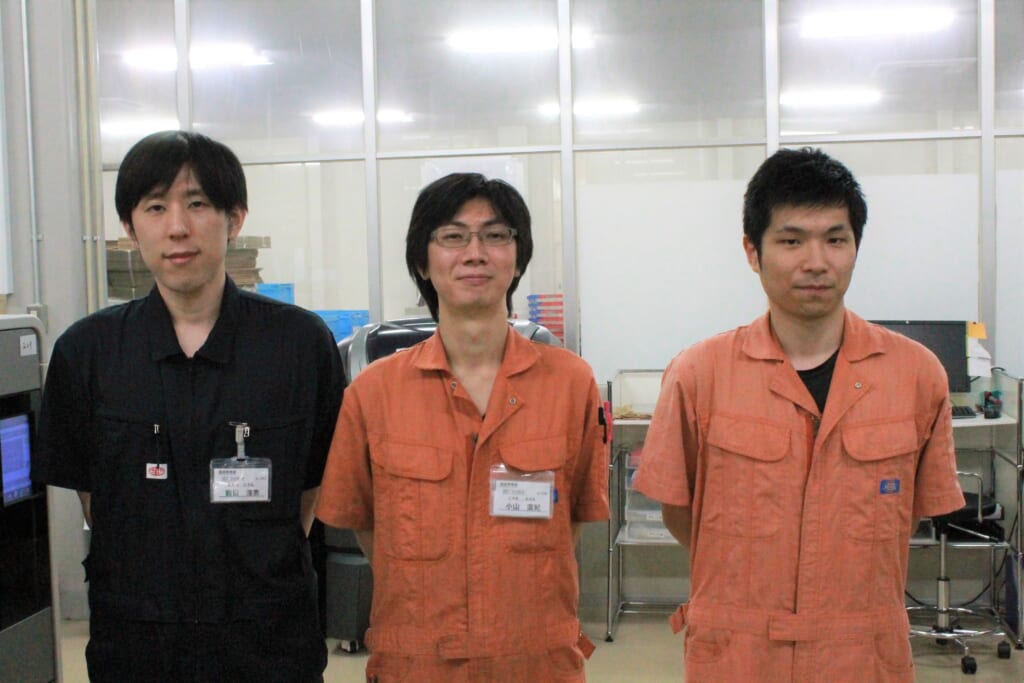
自己紹介と仕事内容について
皆さんの自己紹介と加賀工場で担当している仕事内容をお聞かせいただけますでしょうか。
まずは、小山さんからお願いいたします。
私は2015年度の新卒でDMMに入社しました。
大学で、プログラミングや人間工学、デジタルアーキテクチャといった「モノづくり」に関して総合的に学んだあとで、ラボのほうに入れていただいたことがきっかけです。
所属的には入社から1年後にBase( DMM.com Base )のほうに転籍となっているんですが、入社当初から継続して加賀工場の3Dプリント部門で働いていて、今年で8年目になります。
ありがとうございます。
就職活動で選考を進めるときも、はじめからDMM.makeを志望されていたのでしょうか。
すでに何社か内定をもらっていたのですが、学内求人でDMM.makeの募集を見かけたんです。
話を聞いてみたら3Dプリント事業ではじめて新卒を採るということだったので、面白そうだなと思いまして。
大学でも3DプリントやCGを触る機会があって、モノづくりが好きだったので経験を活かせるのかなと思って、ほかをお断りしてDMM.makeにきました。
ありがとうございます。私も似た境遇で入社したので親近感がありますね。
続いて、東口さんお願いいたします。
私は3Dプリント事業部に来る以前は、DMMの「いろいろレンタル」に関わっていました。
そのときから物流で加賀工場にいて、同じ加賀の物流センターで3Dプリンター事業部を立ち上げるという話が出てきたんです。
その従業員を社内公募で募集すると聞いたので、もともと3Dプリントに興味があったこともあって志願しました。
はじめは「いろいろレンタル」で働かれていたのですね。
3Dプリンターに興味があったということですが、事業部の立ち上げ当初から異動されたのでしょうか。
私が異動したのは3Dプリント事業部が加賀で立ち上がってから1年後の2015年です。
なるほど。3Dプリンターに興味を持たれた理由はなんだったのでしょうか。
専門学生時代にグラフィックデザイン等を学んだりしていて、もともと3Dデータを扱うことに興味があったんです。
3Dを使った仕事に携わりたかったので、3Dプリント事業部の募集があったときはチャンスだと感じました(笑)
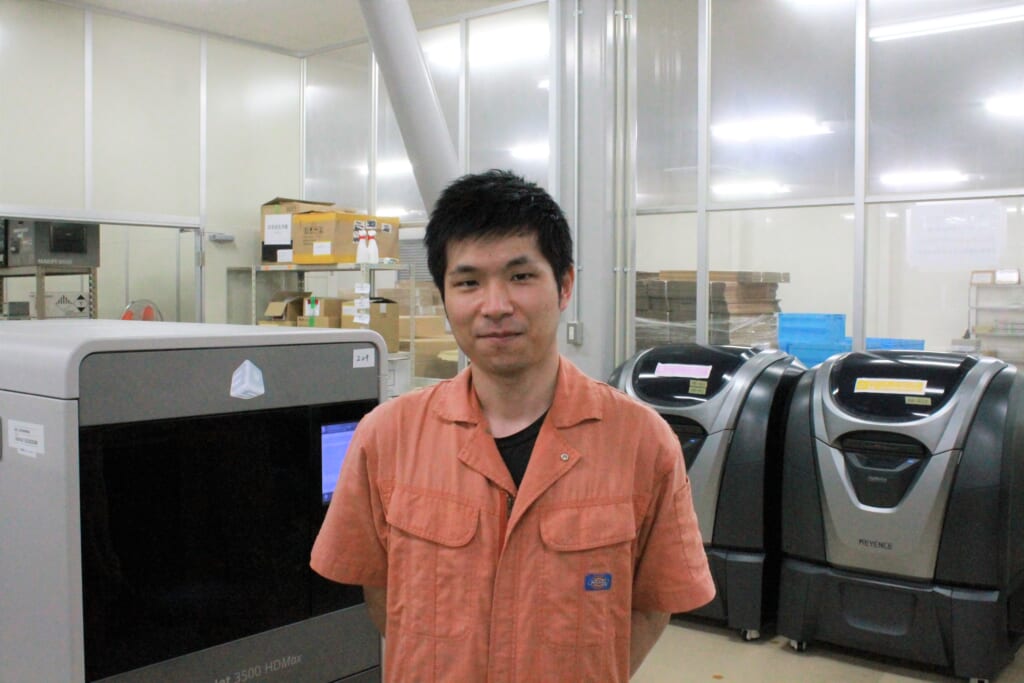
ありがとうございます。
最後に、前田さんお願いいたします。
自分ははじめからDMMに入社したというわけではなくて、卒業してから2社ほど別の仕事を17年くらいしていました。
そこをやめて他の仕事を探そうと思ったときに、3Dプリンターという聞いたことのない異色の仕事と出会って、すごく興味を持ったのがきっかけです。
CGやゲームをやっていて最初から興味もあったので、アルバイトで入社して、その後に正社員になって働いています。
ありがとうございます。
造形部門の皆さんということで、どの機材を担当して、どのような仕事をされているかをお伺いできますでしょうか。
私は主にナイロンとMJF、NXEあたりですね。
あくまで全体的な流れとして、造形の取り出しとか梱包出荷といった全般の業務を担当している感じです。
なるほど。
面付けといいますか、造形のデータ作成は受付班が担当されるのでしょうか。
大まかなイメージとしては、受付班がチェックしたデータを我々がもらうという流れです。
データの内容を理解してどう配置するかを考えて、機械に送信して取り出して、後加工を経た後に梱包して出荷まで担当している感じですかね。
機材の担当とかは縦割りで分担しているイメージになるのでしょうか。
一応、全員がそれぞれの機材を触れるようにはしています。
ただ、大まかには「この人はこの部分」というように割り振って業務を進めています。
なるほど。ありがとうございます。
続いて、東口さんの機材担当とお仕事内容をお聞かせいただけますでしょうか。
私は主にアクリル(ポリジェット)の造形から後加工までを担当しています。
あとは染色する作業や、梱包出荷作業も担当しています。
ありがとうございます。
ポリジェットといえば東口さんという感じですね(笑)
続いて、前田さんお願いいたします。
自分はモデル全般の研磨を担当しています。
あとはMJFの後加工や機械清掃ほかメンテナンスも行っています。
加賀工場でのおおまかな一日の流れ
皆さん共通かもしれませんが、加賀工場での仕事のおおまかな一日の流れを教えてください。
全体の流れとしては、出社したら前日の造形物の取り出しから始まります。
それが終わったら機械を清掃して次のデータを出力できるようにして、取り出した造形物の加工とサポート除去、検品チェックを行って終わったものから梱包して出荷といった流れです。
NEXであればUV硬化など、素材や造形物によってはもう少し工数が増えることもありますが、基本的な流れとしてはだいたいこんな感じです。
造形物を前日にかけられるということは、出荷の後に機械にかけて帰られる感じですか?
基本的には同時並行になります。
出荷をしている裏でデータの作成を詰めて、ものによってはそのままかけて帰ることもありますかね。
なるほど。
梱包作業や出荷作業は全員で分担しているイメージがありますが、シフトは組んでいるのでしょうか。
いえ、そういうわけではないですね。
そのときに手が空いている人が梱包などを行っています。
機材によっても造形時間は変わりますもんね。
長いものだとどれくらいの時間がかかるのでしょうか。
長いものだと48時間くらいかかりますね。造形の後の冷却でさらに数十時間(24~48時間)ほど必要になるので、冷却まで含めると丸四日ほどかかることになります。
造形物の大きさに応じて、かかる時間も長いですね。
NEXだと10〜15分くらいで出力できるので、素材によっても変わってきます。
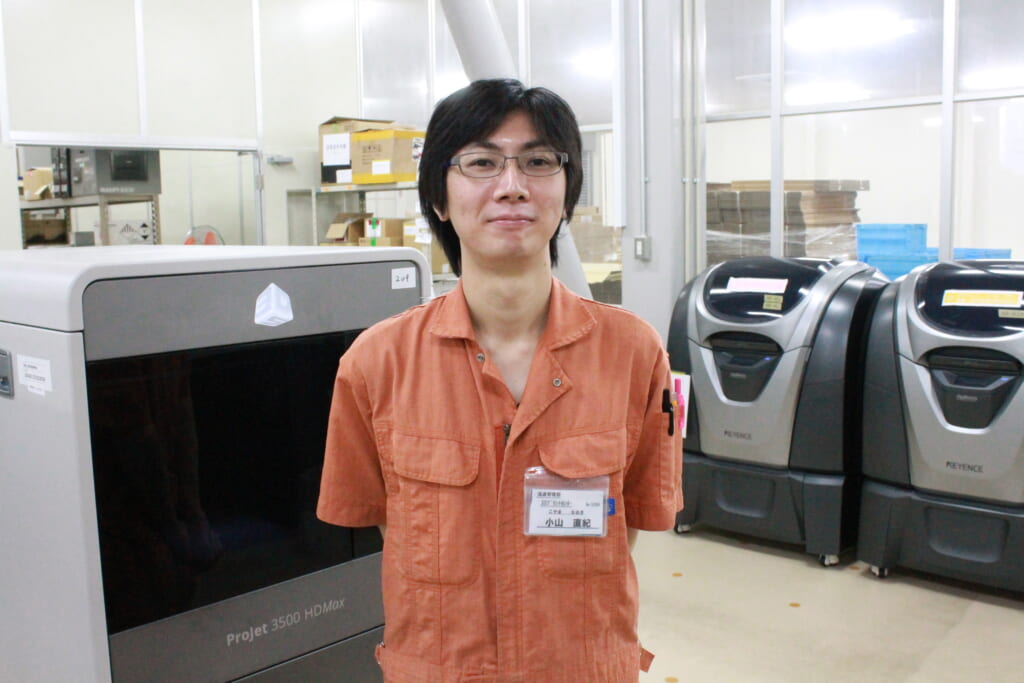
なるほど。
素材の違いでいうと、ナイロンとMJFを比べた場合はMJFのほうが完成までは早いのでしょうか。
そこまで変わらない印象ですね。
造形物の大きさのほうが、完成までの時間への影響が大きくなります。
ありがとうございます。
勝手なイメージですが、SLSは線で熱を加えて、MJFは面で熱を加えるので、MJFのほうが造形までにかかる時間は圧倒的に早いのかなと思っていました。
ナイロンで造形する場合も、基本的には24時間以内に終わるものしか機械にかけないので、その分だけ時間が短くなるのかなと。
MJFは機材がたくさんあって分担するので、一度の造形にかける高さが低いからトータルの時間が抑えられているのかなと思います。
DMM.makeの仕事で得られるやりがい
各々にお伺いしたいのですが、DMM.makeの造形の仕事としてのやりがいを教えていただけますでしょうか。
同じ方法が長く通用しない業界なので、毎日が試行錯誤の繰り返しというところにやりがいを感じますね。
試行錯誤の具体的な内容としてはなにが挙げられるでしょうか。
たとえばNEXは、日の温度や湿度によってバランスが変わってくるんです。
なので、レジンを温める温度を高くしてみたり他のパラメータをいじってみたり、そういった試行錯誤が多いですね。
工場内の室温はエアコンで一定になっているはずなんですが、機械の排気ガスを通じて外気が入ってくる影響で、温度が変わってきてしまうみたいなんです。
温度によって表面が荒れるなどの仕上がりに影響が出てしまうので、良い品質の3Dプリントをお届けするためには、細かい調整が必要になっています。
家庭用の3Dプリンターも環境によって影響を受けますが、産業用だと価格が高いこともあって、そのあたりの調整も自動で行われているイメージが多いかもしれないですね。
続いて、東口さんお願いできますでしょうか。
はい。これは私に限らず全員がそうだと思いますが、注文から出荷までを計画通りに終わらせられたときには達成感があります。
注文がたくさん来るときもあると思いますが、基本的には朝に当日のスケジュールを決めているのでしょうか。
そうですね。本当は全てをその日のうちに終わらせたいと思っているのですが、注文状況や内容によってはできない部分もあります。
難しい部分も多いんですが、そういうところのスケジュール管理にやりがいを感じます。
ある意味、ゲーム感覚ですよね。この注文はこの日までに達成する、みたいな…。
一回の造形にかけるデータをひとつでも多く入れようと考えるのも面白い作業ですよね。
そうですね。ひとつでも多くのデータを配置し、少しでも早くお届けできるようにと日々考えて業務に当たっております。
ポリジェット素材全般は、手作業でデータ1つ1つを配置しているので大変な部分も多いですが、ちょうど空いているスペースに入れられるような受注が入るとカチッとハマって気持ち良いですね。
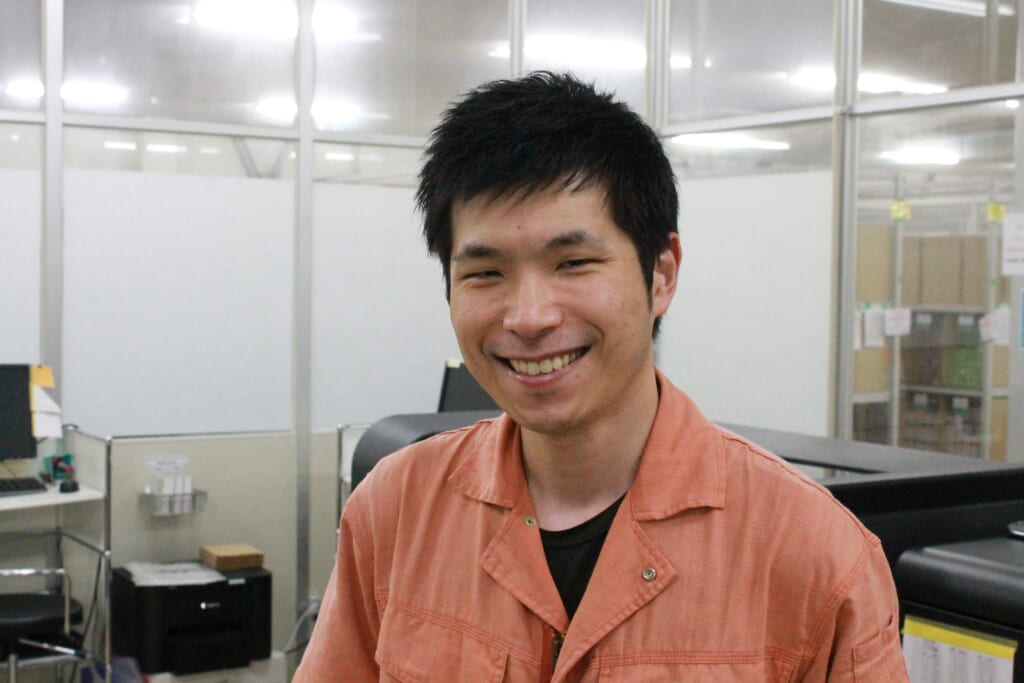
それは気持ち良いですね(笑)
小山さんに戻るんですけど、3Dの空間充填とかはもっと複雑になるのでしょうか。
基本はソフトウェアが自動で組んでくれるので、そこまで複雑ではないですね。
ただ、大変なのが、形によってはどこか一面を犠牲にしないといけないことがあるんです。
どの面を上に向けるかとか、そういうところを考えるのが一番時間がかかって、楽しい部分ではありますね。
自動でとなると、空間充填の最適化のアルゴリズムで勝手な向きで埋まってしまうのでしょうか。
向きはある程度、手動で揃えてから出力する形です。
基本的には、どのデータも「この向きだと一番キレイに出るんじゃないか?」と考えて配置しています。
ただ、それだと出力したパーツの使用用途的にこの向きで出力してほしくなかったというようなご意見もあるので、そういうときは難しいなと感じます。
ありがとうございます。
最後に、前田さんお願いいたします。
僕は、午前中はMJFの取り出しなどが多いんですが、取り出しの時間配分を自分で決めることができるので、それが上手くいったときにはやりがいを感じますね。
普通の工場だと「この時間からこの時間はこの作業をしなさい」みたいに決められていることも多いですもんね。
DMM.makeの仕事に携わっていて大変なこと
次の質問で、仕事をしていて大変だったことは何がありましたか?
普通の工場とは違って、3Dプリントはひとつひとつがオーダーメイドのようなものなんですよね。
画一的な対応が難しいので、品質管理には常に頭を悩ませています。
たとえば、ネジを100本作るという依頼でも、1本1本がオーダーメイドということになります。
検品もひとつひとつ手作業で行っていくので、それでなかなか骨が折れます。
セルという概念があると思うが、何十個もあるデータで一個一個違うと検品がキツいですよね…。
続いて、東口さんお願いいたします。
私の担当のアクリルに限らない話ですが、装置の不調がまったく予測できないことです。
注文の増加が不調のタイミングと重なってしまうと、申し訳ないのですが、どうしても遅延が発生してしまい、お客様にご迷惑をお掛けしてしまう事になり、大変心苦しく感じる部分ではあります。
※ちなみに、アクリル系は最も遅延しない素材の一つです。
ポリジェットだとHDはよく不調になるし、いろいろと大変ですよね。
造形不良が発生したときは再造形をかけることになると思いますが、どんなに調整してもやっぱり不具合は出てしまうのが難しいところですよね。
出ちゃうときは出ちゃいますね…。
そのときは体感でマシンの調整をしたり、造形方向を変えたり等を試しています。。
マシンメンテナンスなどで注文が山ほど溜まっている時は、どの注文を優先するかとか、造形時間を考慮しながらスケジュールを組むのが難しいですね。
ありがとうございます。
前田さんはいかがでしょうか。
自分はバレル研磨のことなんですが、磨けば磨くほどキレイになるものの、それにともなって破損率もあがってしまうんですよね。
先ほどもお話に出たように、3Dプリントの造形物はオーダーメイドで、まったく同じ品物がない。
それによって割合とか時間を変えないといけないんですが、実際に出力してみないとわからないので、経験則などでいろいろと考えながら調整するのが大変だと感じます。
バレル研磨を行うのは一注文ごとですか?
ある程度まとめて研磨を行うのでしょうか?
形状によっては単体で研磨することもありますが、基本的には同じ素材でまとめて研磨しています。
違う素材同士を混ぜてしまうと他の造形物に色がついてしまうので、そのあたりはしっかり分けて研磨しています。
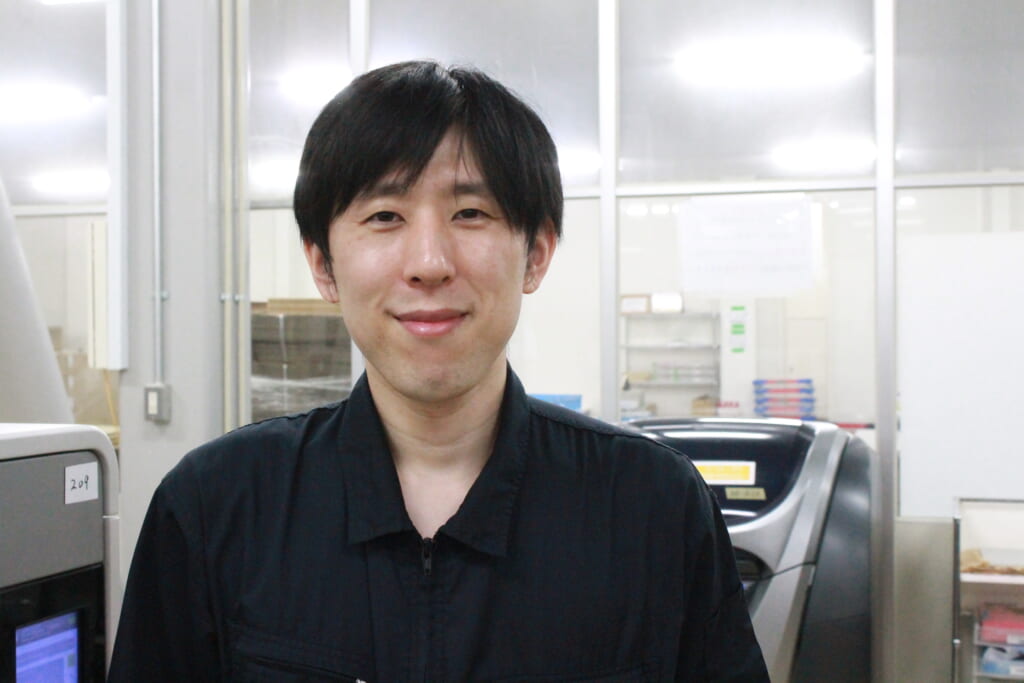
DMM.makeで働いていてよかったこと
DMM.makeで働いていてよかったと感じることを教えていただけますでしょうか。
3Dプリントでは、老若男女、さまざまな人が注文をしてくれるので、本当にいろいろな3Dモデルを目にできるんです。
フィギュアから工業製品まで、たくさんのデータを見れるのがすごく良い刺激になっています。
データをみて、この造形物がどう使われるのかを想像するのも楽しいですね。
受付班の話でも似たお話が出てました(笑)
ツイッターでアップロードされた造形物を見ると楽しいというお話がありましたね。
個人的にSNSを見ていて、「あ!これ!」ってなるとすごく嬉しくなります(笑)
東口さんはいかがでしょうか。
3Dプリントというもの自体がモノづくりの中で最先端の業界だと思っているので、そこに携われていることが嬉しいです。
今後も3Dプリントは成長していくと思っているので、一緒に業界の成長を見ていけるのが良いところだなと感じています。
ありがとうございます。
前田さんもお願いいたします。
自分も毎回モデルを見るたびに、みなさんの想いが込められているのを感じています。
そういった想いを受け取って、さらに良くしてお客様に提供したいなという気持ちになります。
そういう気持ちが持てるのはこの仕事をしていて良かったなと感じます。
「想い」を表現できるというのはいいところですね。
やはり、データを見ていてお客様の想いを感じる部分は多いのでしょうか。
ありますね(笑)
見るからに試行錯誤したんだろうなというデータは多いです。
作り込んでいるデータですか?
同じデータが入ってくることもあるんですが、よく見ると少しだけ仕様が変わっていることもあります。
そういうのを見つけると「この部分はこだわりがあるんだなぁ」とか「試行錯誤してるんだなぁ」と思います(笑)
なるほど。
ポリジェットはひとつひとつを手作業でやっているから、データの内容はより覚えてそうですね。
皆さんのこだわりの塊なので、良い記憶も悪い記憶もあります(笑)
DMM.makeの良いところ
造形の皆さんの目線で、DMM.makeのサービスとしての良いところを教えていただけますでしょうか。
さっきの話と若干かぶるところがあるんですが、ライトユーザーからヘビーユーザーまで活用できる環境が提供されているのは良いところだなと感じます。
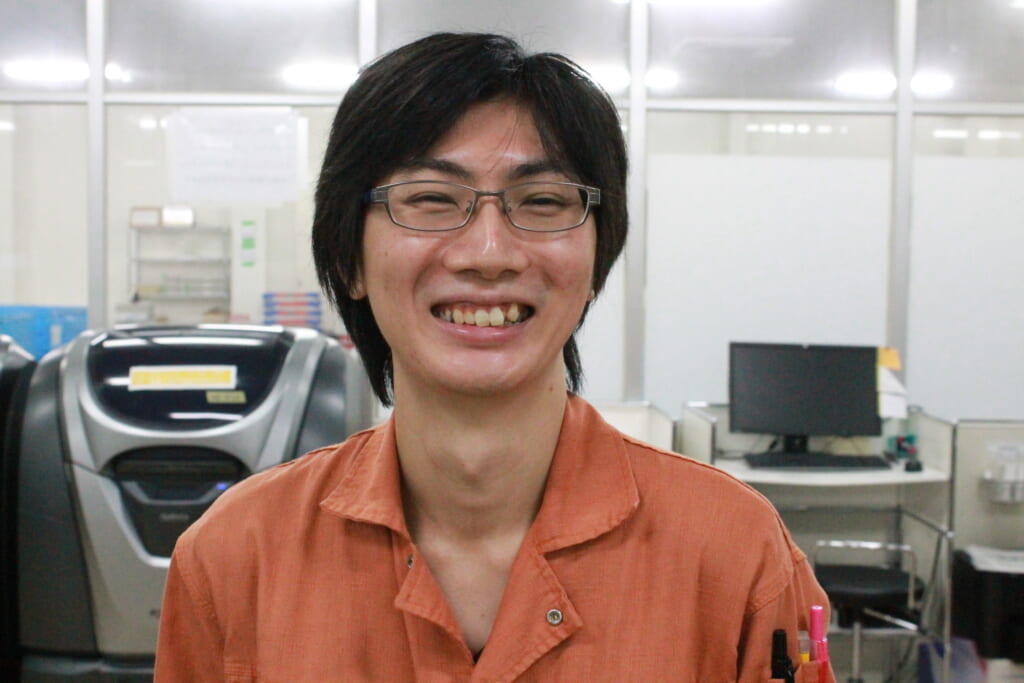
他のサービスと比べてもハードルが低めですもんね。
通常だと見積もりを取って見積書を送ってもらってというメールのやりとりが、Webだけで完結するのはいいところですよね。
私も似たような考えを持っています。
法人のお客様に限らず、一般のお客様にも利用しやすいのが良い点だなと。
その最たるものが「クリエイターズマーケット」で、3Dデータを作れないお客様でも気軽に3Dプリンターで造形したモノを手にできるのはすごく良いサービスだと思います。
そうですよね。3Dを使った造形物って、一般的にどこかお店に行けば手に入れられるものではないですもんね。
昔と比べて、徐々に増えてきてはいるものの、お店じゃ全然見かけないですし。
前田さんもDMM.makeの良いところを教えていただけますでしょうか。
自分は少し視点が違うかもしれないですが、前に働いていた会社と比べて、とりあえず試させてくれる社風がすごく良いなと感じます。
他社にいた頃、自分が意見を出しても「会社の決まりだから我慢してほしい」ということが多かったので…。
DMM全体としての魅力ですよね(笑)
私も、とりあえず試させてくれる環境がDMM.makeのサービス向上につながっているのかなと感じます。
最後にお客さまへお伝えしたいこと
最後に、いま担当している仕事も含めて、今後の仕事に対する意気込みや想いをお聞かせいただけますでしょうか。
常日頃からより良い品質にしていこうという想いで業務に取り組んでいます。
お客様に満足してもらえるように新しい情報を仕入れて、実際に試してという試行錯誤は今後も継続して行っていきたいですね。
私は後加工の正確さなどをもっと上げていきたいと思っています。
お客様が想いを込めて、こだわって作ったデータに限りなく近付けた状態でお届けできたら良いなと。
もっと早く、もっとキレイに仕上げられるように追求していきたいです。
産業のプリンターだと、ナレッジというかノウハウがネットに載っていないので、本当に自分で試行錯誤していかないといけないですよね。
前田さんもお願いいたします。
いまやっていること以上にクオリティを上げていって、今まで以上にお客様に喜んでいただきたいと思っています。
あとは、自分自身も3Dプリントで作ってみて、作る側の視点で見てどう感じるかを考えながら、3Dプリントというものをもっと広げていきたいなと。
日々の仕事だけじゃなくて、自分でも3Dプリンターを活用したいということですね。
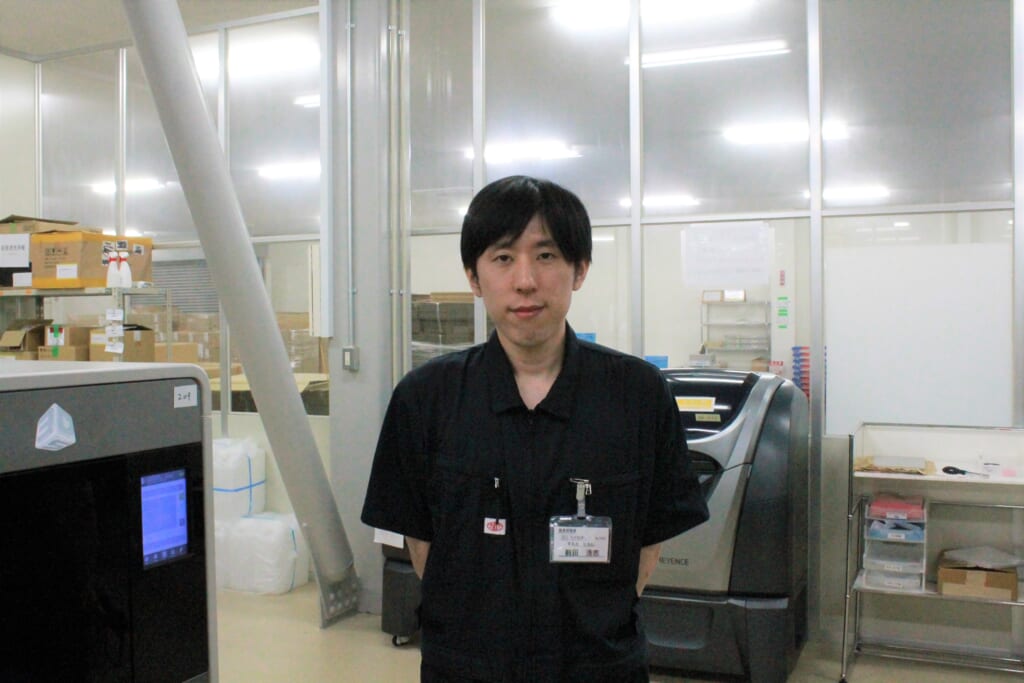
DMM.makeを使っていただいているお客様へのメッセージ
最後に、DMM.makeをご利用いただいているお客様へ、メッセージをお願いいたします。
品質には万全を期しているんですけれども、お客様の用途によってはご納得いただけない出来になってしまうこともあるかと思います。
そういうときは遠慮なく仰っていただければと思います。今後もよろしくお願いいたします。
アクリルなどはデータを作り込めば作り込むだけ高精細になります。
お客さまのこだわりに負けないくらいのこだわりを持って携わっていきたいと思っています。
3Dデータを作ることのハードルが高いと思っている人が多いと思いますが、少しでもそのハードルを下げて、サポートができればと思っています。
なので、ぜひ気軽に注文していただければ嬉しく思います。
我々一同、お客様にご満足いただけるように尽力しているので、ぜひ気軽にご利用いただきたいですよね。
それでは、本日は以上とさせていただきます。ありがとうございました。
ありがとうございました。
ありがとうございました。
ありがとうございました。